Quality assurance (QA) and quality control (QC) are cornerstones of consistent product integrity and customer satisfaction. However, in many organizations, especially those operating across both regulated and non-regulated sectors, QA and QC practices vary significantly, leading to inefficiencies, compliance risks, and unpredictable outcomes. Standardizing these processes through well-defined standard operating procedures (SOPs) ensures clarity, accountability, and repeatability. Whether you operate in pharmaceuticals, manufacturing, food processing, or tech services, unified QA and QC SOPs help align teams, streamline audits, and reduce operational errors. For regulated industries, standardized SOPs are often legally mandated, while in non-regulated spaces, they establish best practices that enhance competitiveness and reliability. More importantly, they bridge gaps between compliance and continuous improvement, supporting quality at every stage, from design to delivery.
This article will compare quality control and assurance SOPs, exploring their key elements and the steps to implement them.
Quality Control SOP vs Quality Assurance SOP
Understanding the distinction between quality control SOP and quality assurance SOP is essential for maintaining compliance, consistency, and product integrity. Both serve different purposes within a quality management system, yet they are often confused.
Quality Control SOP
A quality control SOP is a documented set of step-by-step instructions that outline how to inspect, verify, and ensure product or service quality throughout the production or service delivery process. It standardizes procedures for measuring, monitoring, and recording quality parameters, enabling consistent output that meets predefined specifications and regulatory standards.
Manufacturers, laboratories, healthcare providers, construction firms, and food processors require QC SOPs to maintain product integrity and compliance with internal and external standards. You need a QC SOP when:
- Launching a new product or service
- Implementing ISO, GMP, HACCP, or other compliance systems
- Experiencing quality failures or increased customer complaints
- Scaling production or outsourcing operations
- Training new staff or standardizing existing processes
Implementing a QC SOP yields measurable improvements across operations:
- Ensures uniform inspection and testing across batches or sites.
- Aligns your processes with regulatory and certification requirements.
- Documents procedures, test results, and corrective actions for audits.
- Minimizes human error and subjective decision-making.
- Streamlines training, reduces rework, and prevents wastage.
- Enhances product reliability and strengthens your brand.
QC SOPs should be developed based on risk assessment and critical control points. Start by defining what to measure, how to measure it, and acceptable quality limits. Involve quality assurance teams, production leads, and regulatory experts to align technical and operational requirements.
The primary purpose is to provide clear, repeatable instructions that ensure each unit of output meets quality standards. It also serves to protect your brand reputation, ensure compliance, and enable data-driven improvements.
A QC SOP typically covers:
- Inspection points: Raw materials, in-process checks, final products
- Testing methods: Mechanical, chemical, microbial, or functional tests
- Acceptance criteria: Tolerances, thresholds, and pass/fail conditions
- Documentation: Logs, checklists, forms, and digital records
- Corrective actions: Procedures for handling deviations and nonconformities
- Review cycles: SOP revision timelines, change control, and approvals
Quality Assurance SOP
A quality assurance standard operating procedure is a structured document that outlines precise methods, responsibilities, and quality control measures to ensure that a product or service meets predefined standards. It defines how to consistently execute tasks, monitor outcomes, and implement corrective actions to uphold quality benchmarks across all stages of a process.
Regulated industries such as pharmaceuticals, biotechnology, food manufacturing, healthcare, aerospace, and automotive require QA SOPs at all operational levels.
You need them when:
- Launching a new product or service.
- Standardizing multi-site operations.
- Complying with regulatory frameworks (e.g., FDA, ISO 9001, GMP).
- Training staff to ensure uniform quality practices.
- Introducing automation or process changes.
QA SOPs offer several benefits, including the following:
- Eliminate ambiguity by providing clear steps that ensure all personnel follow the same procedures, maintaining product consistency and regulatory compliance.
- Identify control points, helping you detect errors early and reduce the likelihood of product recalls, legal penalties, or reputational damage.
- Defined procedures streamline workflows and improve resource allocation, minimizing trial-and-error and reducing rework.
- New employees onboard faster with documented procedures. Clear roles and responsibilities also enhance accountability and performance tracking.
- Provide a foundation for data-driven quality assessments. You can audit, revise, and optimize procedures based on real metrics and outcomes.
Your QA SOP should follow a process-based approach, aligning with company standards, client requirements, or legal mandates. Identify critical control points in each workflow and include checkpoints for monitoring and verification. Document approved tools, techniques, and parameters, and use performance data and audits to refine SOPs over time.
The primary purpose is to ensure systematic quality assurance through transparent, traceable, and standardized practices. It protects your operations from deviations and supports strategic goals like customer satisfaction, brand reputation, and compliance.
A QA SOP covers:
- All personnel involved in the production or service process.
- All stages from raw material intake to final product delivery.
- Specific procedures like sampling, inspection, calibration, corrective actions, documentation control, and change management.
- Integration with related SOPs in production, safety, and maintenance for a unified quality framework.
Aspect | Quality Control SOP | Quality Assurance SOP |
Definition | Step-by-step guide for inspecting, verifying, and validating product quality. | Structured document for ensuring quality standards are maintained across processes. |
Primary Focus | Detects and corrects defects during or after production. | Prevents defects by standardizing processes and responsibilities. |
Approach | Risk-based, centered on critical control points and measurable outcomes. | Process-based, focused on mapping workflows and ensuring system-wide quality consistency. |
Purpose | Ensure each unit meets technical and regulatory standards. | Establish systemic quality through traceable and standardized practices. |
Scope | Inspection points, testing methods, acceptance criteria, and corrective actions. | Personnel roles, process stages, audits, documentation, and change control. |
Who Needs It | Manufacturers, labs, healthcare, food processors, and construction firms. | Pharma, biotech, aerospace, healthcare, automotive, and other regulated industries. |
When to Use | New product launch, scaling operations, increased defects, and regulatory compliance. | New processes, automation, multi-site standardization, and regulatory audits. |
Key Benefits | Consistency, compliance, traceability, reduced errors, cost savings, and higher satisfaction. | Risk reduction, operational efficiency, accountability, faster training, and continuous improvement. |
Compliance Role | Ensures final outputs align with internal and external quality requirements. | Embeds quality into every process to meet compliance from start to finish. |
Training Function | Helps train staff on inspection procedures and acceptance limits. | Facilitates onboarding and performance consistency across roles. |
Improvement Driver | Identifies and corrects deviations at inspection points. | Enables audit-based revisions and long-term process optimization. |
Key Elements of Quality Control & Quality Assurance SOP
Here are the important components you must include in your QA or QC SOP to maintain operational effectiveness and accountability.
Purpose, Scope, and Definitions
Define the SOP’s primary aim, i.e., to standardize QA and QC practices, ensuring product safety, efficacy, and compliance with regulatory and internal standards. Clearly delineate the functional and departmental boundaries. This SOP should apply across procurement, production, quality control labs, packaging, and distribution within your facility.
Include precise definitions for key terms such as:
- Deviation: Unplanned departure from SOP or process
- CAPA: Corrective and Preventive Actions
- OOS: Out of Specification
- QA vs. QC: QA is process-oriented; QC is product-oriented
Roles and Responsibilities
Clearly outline reporting hierarchies and escalation protocols by defining and assigning responsibilities across departments.
- Quality Assurance Manager: Oversees implementation, training, compliance, and continuous improvement.
- Quality Control Analysts: Execute testing, report results, and flag anomalies.
- Production Supervisor: Ensures process adherence and reports deviations.
- Supply Chain/Procurement: Selects and audits vendors against quality criteria.
- Regulatory Affairs: Aligns SOPs with current regulatory requirements.
Quality Standards and Criteria
Include measurable benchmarks and direct references to applicable clauses from ISO 9001 and GMP guidelines:
- Raw Material Acceptance: ISO 9001:2015 Clause 8.4; 21 CFR 211.84
- In-Process Control: ICH Q8 (R2), GMP Chapter 4
- Product Release: 21 CFR 211.165, ISO 13485 Clause 7.3.7
Key performance indicators (KPIs) that should be tracked monthly and reviewed quarterly include
- Batch rejection rate (%)
- Vendor non-conformance rate (%)
- CAPA closure time (days)
- Internal audit finding recurrence rate (%)
Documentation and Recordkeeping
A comprehensive documentation system ensures traceability, regulatory compliance, and data integrity across the quality lifecycle. All critical records, including batch manufacturing records, laboratory results, audit reports, and change control logs, should be securely maintained. Track revisions, authorship, effective dates, and reasons for change. Regulatory alignment with ISO 9001 Clause 7.5 and 21 CFR Part 11 reinforces the credibility and admissibility of documented evidence.
Procedures and Steps
Every key quality activity must follow a documented and controlled process to ensure repeatability and compliance. For raw material and supplier quality, pre-qualification, certificate verification, and periodic audits form essential components. In-process controls are maintained through real-time parameter checks and statistical monitoring, while finished product quality is confirmed against approved specifications. These procedures, supported by structured workflows and escalation protocols, prevent errors and protect product integrity.
Deviation and Change Management
All deviations from procedures or specifications are documented and analyzed to determine the root cause and impact. Categorization into minor or major deviations supports appropriate escalation. Change control processes assess the potential risks of modifications and require documented approvals before implementation. CAPA is used to address and prevent recurring issues through structured investigation and effectiveness checks.
Procedures for Audit, Inspection, and Quality Reviews
Audits and inspections help verify compliance with established standards and identify areas for improvement. Internal audits are scheduled and executed using objective criteria and structured checklists. Regulatory inspections require preparedness through predefined roles and timely documentation. Management reviews analyze audit trends, CAPA outcomes, and quality metrics to guide strategic decisions.
Risk and Compliance Management
Risk assessment tools such as FMEA or HACCP help identify potential failures and assess their impact on product quality. Each risk is evaluated based on likelihood and severity to prioritize mitigation efforts. Compliance is maintained through ongoing monitoring of regulatory updates, periodic gap assessments, and adherence to internal controls aligned with industry standards.
6 Steps to Develop & Implement QA and QC SOPs
Each step in the process of developing and implementing QC and QA SOPs must align with your organization’s quality goals, regulatory requirements, and operational capabilities. Here’s how to approach it effectively:
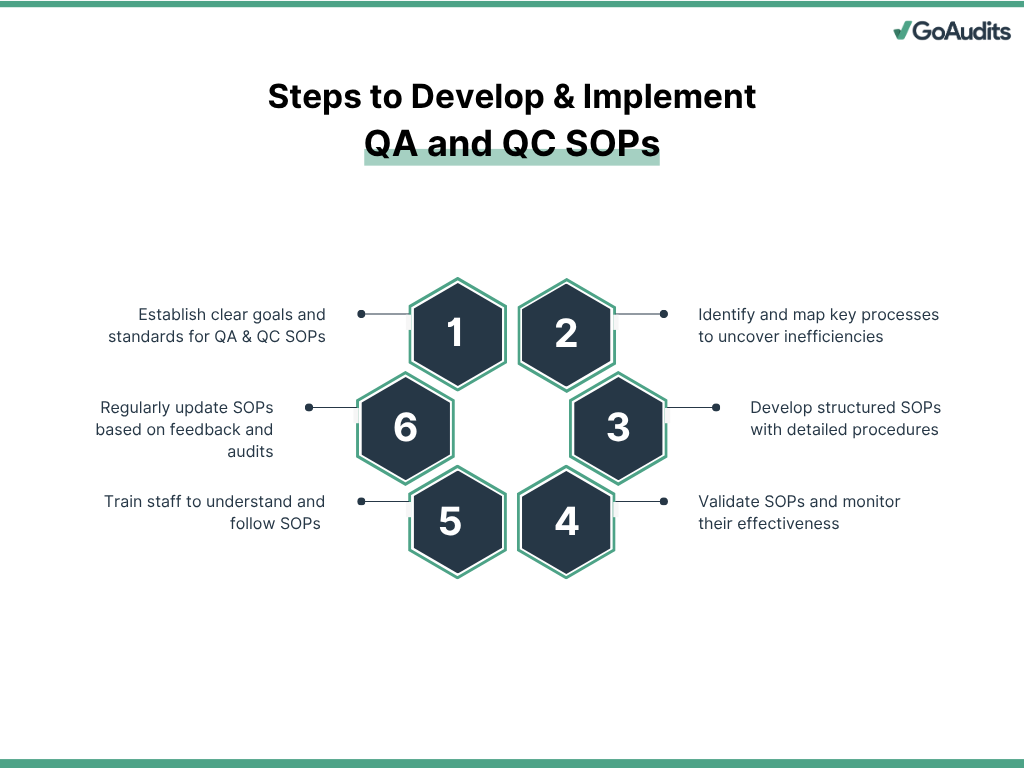
1. Define Objectives, Requirements, and Quality Standards
Start by clearly defining the objectives of your QA and QC SOPs. Establish what your organization aims to achieve, whether it’s regulatory compliance, product consistency, risk reduction, or process optimization.
Identify applicable regulatory requirements and internal quality benchmarks. Set measurable quality standards tailored to your product, service, and industry. These standards will serve as reference points throughout SOP development.
2. Identify and Analyze Key Processes
Perform a gap analysis to uncover discrepancies between current practices and desired quality standards. This highlights areas that lack standardization or pose compliance risks.
Form a cross-functional team including QA & QC personnel, operations managers, and process owners. Their collective insights ensure SOPs reflect actual workflows and address practical challenges.
Map current workflows step-by-step. Document what is being done, by whom, and how. Use flowcharts or diagrams to visualize the sequence and interdependencies. This process exposes inefficiencies and opportunities for improvement.
3. Draft the QA & QC SOPs
Develop a structured SOP framework with clearly defined sections (purpose, scope, responsibilities, materials required, procedure steps, and references). Use consistent formatting and simple, direct language to ensure clarity.
Write detailed procedures for each QA and QC task. Define roles, timelines, tools, acceptance criteria, and documentation protocols. Avoid ambiguity; each instruction should leave no room for interpretation.
Include quality checkpoints, control limits, and criteria for escalation. Specify how results will be recorded, analyzed, and reviewed.
4. Review, Implement, and Monitor
Conduct a comprehensive review of the drafted SOPs with key stakeholders. Validate their accuracy, relevance, and feasibility. Address all feedback before final approval.
Use digital checklists tied to each SOP for on-the-ground use, reinforcing procedural adherence and simplifying monitoring. Checklists must mirror SOP steps exactly to ensure accountability and traceability.
👉 Free Resources
GoAudits offers a wide range of ready-to-use quality assurance and quality control checklists tailored for different industries. You can sign up for free and start using these checklists to streamline QA and QC processes while ensuring full compliance with industry-specific standards.
→ Food Quality Control Checklist
→ Construction Quality Control Checklist
→ Production Quality Control Checklist for Manufacturing
→ Construction Quality Inspection
→ Clothing Quality Control Checklist
→ Fabrication Quality Control Checklist
→ Manufacturing Quality Control Checklist
→ Manufacturing Process Audit Checklist
→ Free Hotel Quality Checklists
Once implemented, monitor compliance and effectiveness. Track performance indicators, error rates, and corrective actions. Regular monitoring helps detect deviations early and maintain quality standards.
5. Train Staff Thoroughly
Deliver role-specific training to ensure that each team member understands and follows the SOPs. Use hands-on sessions, job aids, and competency assessments to reinforce learning. Document all training activities and evaluate their effectiveness periodically. Re-train as needed, especially after updates or audit findings.
6. Continuous Improvement
Collect user feedback on SOP clarity, practicality, and effectiveness. Encourage teams to report challenges and suggest improvements. Conduct regular internal audits to assess SOP compliance, identify risks, and uncover improvement areas. Ensure audit findings lead to actionable changes. Update SOPs promptly in response to changes in regulations, processes, or tools. Version control and document tracking are essential to maintain current and authoritative SOPs.
Digitize Your Quality Assurance & Quality Control SOPs with GoAudits
GoAudits is an all-in-one platform built to simplify inspections, streamline compliance, and strengthen accountability. Eliminate paper-based workflows, reduce manual errors, and make data-driven decisions with ease. Whether you manage daily operations or oversee multi-site audits, GoAudits quality inspection software transforms how you manage QA and QC SOPs. Use mobile inspections to capture structured data, automate reporting, assign corrective actions, and analyze results in real time. It minimizes training time, maximizes efficiency, and helps ensure compliance at every level.
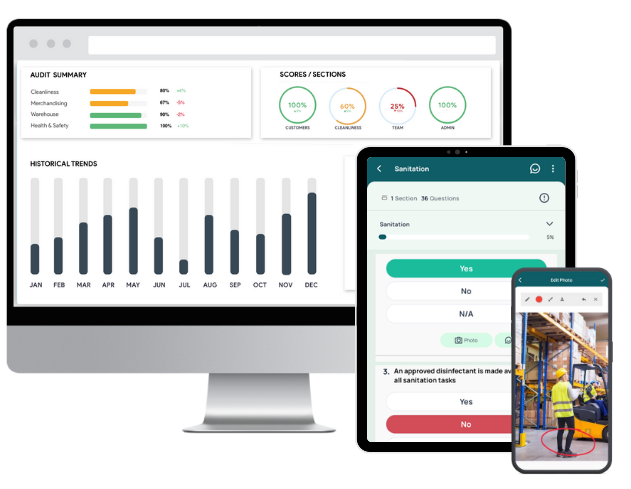
- Access a rich library of industry-specific templates, or upload your own to start inspections immediately. Send us your checklists and we’ll digitize them for you at no additional cost.
- Conduct inspections from any location using your preferred device. No internet? No problem. Work offline and sync your data later.
- Generate branded, professional quality control reports automatically at the end of each inspection. Include photos, timestamps, signatures, and geo-tags, and share them with relevant stakeholders.
- Assign tasks directly during inspections. Set priorities, due dates, and responsibilities. Ensure full accountability and continuous improvement.
- Automate task assignments, notifications, and report distribution. Build workflows to streamline approvals and corrective action tracking.
- Access smart dashboards for trend analysis. Monitor audit scores, identify recurring issues, and make informed decisions based on real-time data.
GoAudits enabled Nissin Foods to overhaul its quality‑control inspections by digitizing dozens of daily GMP, HACCP, and product integrity audits across its manufacturing facilities. Previously reliant on paper forms, manual scanning, and signature gathering, Nissin Foods faced delays in filing reports or triggering corrective actions. With GoAudits’ mobile and desktop platform, inspection teams now log results and corrective actions in real time. Reports are generated instantly and shared with relevant stakeholders, streamlining workflows and enabling faster issue resolution.
👉 Nissin Foods has achieved over 96 % completion rates for GMP audits and enjoys customized matrix reporting and dedicated customer support tailored to its facilities, boosting visibility of trends and enhancing operational efficiency.
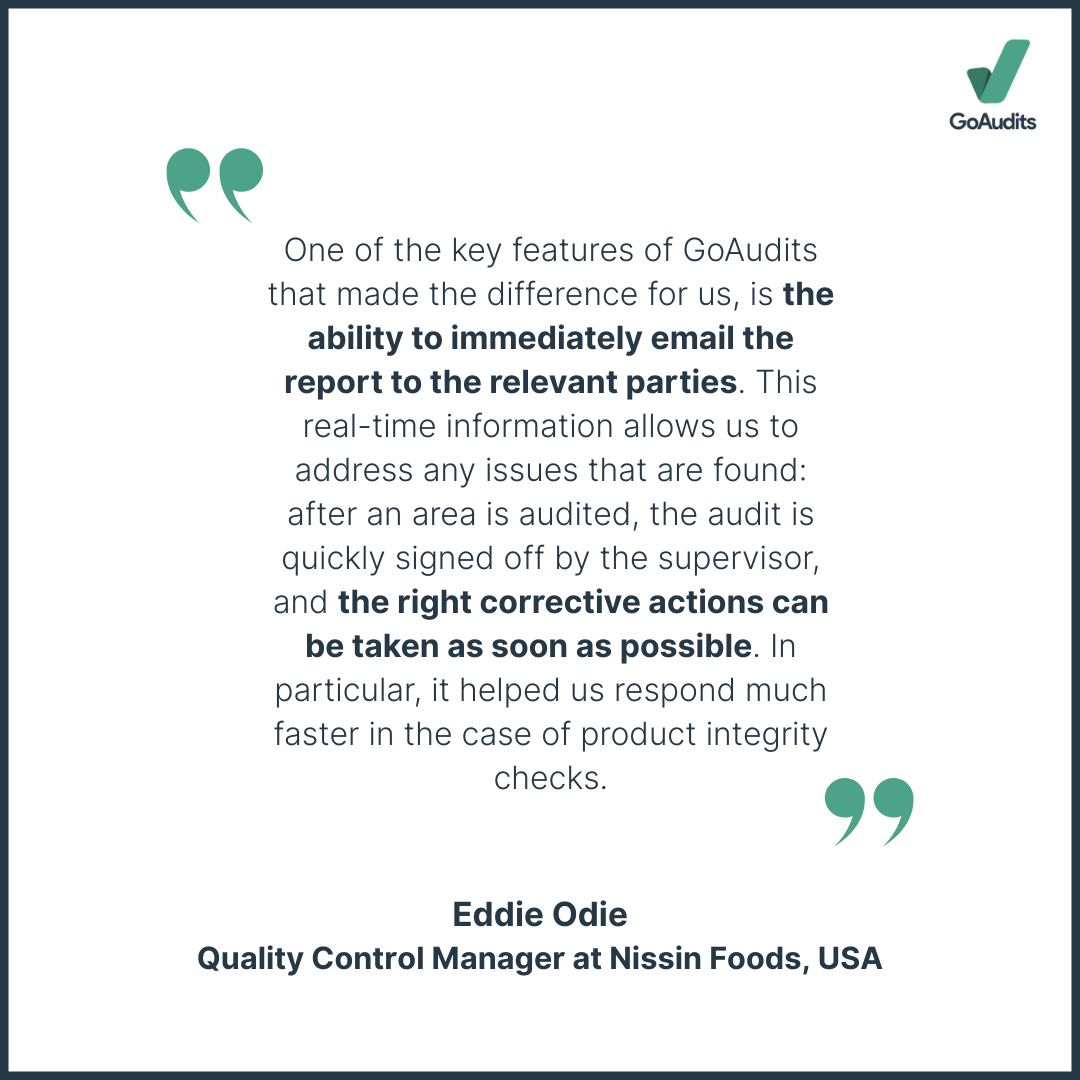
QA & QC SOP Examples by Industry
Below are industry-specific QA and QC SOP examples.
Manufacturing
QA and QC SOPs help maintain consistent product quality across production batches while meeting ISO 9001 or other applicable standards. Key components include:
- Raw Material Inspection: Verify supplier certifications, conduct sampling tests, and document material conformity.
- Process Control SOPs: Define machine calibration frequencies, operator qualifications, and process validation criteria.
- In-Process Checks: Outline parameters (e.g., dimensions, weight, functionality) and frequency of inspections at critical control points.
- Non-Conformance Management: Standardize reporting, root cause analysis, and corrective and preventive actions.
- Final Product Testing: Specify functional, visual, and stress tests before packaging and release.
- Documentation Protocol: Maintain real-time logs, traceability records, and batch reports.
👉 Free Resources
GoAudits manufacturing quality control software offers an extensive library of manufacturing audit checklists, aligned with manufacturing SOPs, to standardize inspections, streamline compliance, and reduce production defects.
→ SQFI Quality Checklist
→ Manufacturing Quality Control Checklist
→ Quality Control Audit Checklist
→ Vendor Quality Audit Checklist
→ Quality Control Incoming Inspection Checklist
Construction
The goal is to ensure that construction projects meet structural integrity, safety codes, and contractual specifications. Key components are:
- Material Verification: Define procedures for sampling and testing aggregates, concrete, steel, etc., with compliance to ASTM or equivalent standards.
- Site Inspection Plans: Detail inspection schedules for excavation, formwork, rebar placement, and concrete pours.
- Workmanship Standards: Include measurable tolerances and approved techniques for each trade (e.g., masonry, plumbing, electrical).
- Third-Party Testing: Establish protocols for engaging certified labs for soil, concrete, and weld testing.
- Change Control: Govern documentation, review, and approval of design deviations or specification changes.
- Handover & Commissioning: List final inspections, snagging, client approvals, and sign-off requirements.
👉 Free Resources
GoAudits offers detailed construction inspection checklists to ensure quality assurance and control in construction. Alternatively, you can also digitize your construction SOPs into checklists.
→ Construction Quality Control Checklist
→ Construction Quality Inspection
→ Concrete Quality Control Checklist
→ Quality Control Checklist for Road Construction
→ Residential Construction Quality Control Checklist
Healthcare
Standardized QA and QC procedures ensure patient safety, clinical accuracy, and regulatory compliance (e.g., with JCI, NABH, or HIPAA). Key components include:
- Clinical Procedure Standardization: Define steps for diagnostics, surgeries, and patient care with control checklists.
- Equipment Calibration SOPs: Schedule maintenance and calibration of diagnostic, surgical, and life-support equipment.
- Sterility Assurance: Establish disinfection protocols for tools, operating rooms, and ICUs using verifiable methods (e.g., biological indicators).
- Patient Data Quality: Ensure accurate, secure, and real-time health record entry with audit trails.
- Incident Reporting System: Include structured formats for documenting, investigating, and correcting adverse events or near misses.
- Internal Audits: Detail periodic QA reviews across departments with compliance tracking mechanisms.
👉 Free Resources
GoAudits supports healthcare facilities with customizable clinical audit checklists, enabling consistent quality assurance across procedures, patient care, infection control, and operational compliance.
→ Patient Care Checklist
→ Infection Control Audit Template
→ Hospital Room Cleaning Checklist
→ Patient Satisfaction Survey Template
→ QAPI Plan Template
Food & Beverage
To guarantee food safety, hygiene, and product consistency in compliance with HACCP, ISO 22000, or FSSAI standards. Key components are:
- Ingredient Verification: Specify tests for allergens, pesticides, moisture content, and microbial limits.
- Environmental Monitoring: Include air and surface sampling schedules, swab tests, and cleaning validations.
- Batch Production Controls: Define temperature, time, and pH checkpoints with real-time monitoring and deviation handling.
- Sensory Evaluation SOPs: Standardize protocols for taste, texture, aroma, and appearance assessment.
- Packaging & Labeling Verification: Confirm compliance with regulatory labeling (e.g., nutritional information, expiry dates).
- Recall & Traceability Procedures: Map out traceability systems and rapid recall execution protocols.
👉 Free Resources
GoAudits offers a wide range of food safety audit checklists to ensure QA and QC in the food industry, covering every aspect from raw material inspections to packaging, hygiene audits, and product quality verification. You can also digitize your food SOPs into checklists.
→ Food Safety Checklists & Audit Templates
→ BRC Audit Checklists
→ Food Quality Control Checklist
→ Vendor Quality Audit Checklist
→ GMP Audit Checklist Templates
Pharmaceuticals
QA and QC SOPs ensure product safety, efficacy, and regulatory compliance with GMP, USFDA, or EMA guidelines. Here are the key aspects:
- Raw Material Qualification: Define identity, purity, potency, and supplier validation checks.
- Manufacturing Process Validation: Include detailed protocols for critical process parameters (CPPs) and critical quality attributes (CQAs).
- Sterility Testing: Outline aseptic techniques, cleanroom classifications, and microbial testing methods.
- In-Process and Final Product Testing: Standardize dissolution, content uniformity, and stability testing.
- Deviation & Change Control: Establish clear documentation routes and review boards for evaluating process changes.
- Data Integrity SOPs: Govern electronic record keeping, audit trails, and ALCOA+ compliance.
FAQ
Quality control is considered reactive because it identifies defects only after a product is manufactured or service is delivered. It involves inspection, testing, and verification activities that occur post-production to detect non-conformities. In contrast, quality assurance is proactive as it focuses on preventing defects through systematic planning, process controls, and audits during development. While QA aims to build quality into the process, QC responds to errors that have already occurred, making it a corrective rather than a preventive measure.
QA and QC work together by covering both the prevention and detection of quality issues. QA establishes the framework (policies, procedures, and process standards) to ensure quality is built from the start, while QC executes tests and inspections to validate the final output. QA reduces the likelihood of defects occurring, and QC ensures any remaining issues are identified before reaching customers. This strengthens compliance, enhances reliability, and minimizes risks within the quality management system.
SOPs drive consistency by providing clear, step-by-step instructions for executing tasks uniformly across teams and processes. This minimizes variation, reduces errors, and ensures compliance with regulatory and internal quality standards. SOPs also improve efficiency by streamlining workflows, eliminating ambiguity, and reducing the learning curve for new employees. As a result, they enable faster decision-making, better resource management, and continuous improvement within the quality management framework.
An SOP QC checklist is a structured document that outlines specific quality control tasks aligned with a particular standard operating procedure. It ensures that each QC step, such as measurements, visual inspections, or functional tests, is executed as required. A QC checklist helps maintain procedural integrity, document compliance, and verify that the final product meets predefined quality criteria. It also supports traceability, audit readiness, and continuous quality monitoring by standardizing inspection and verification efforts.