Key Takeaways
- QA and QC in construction ensure projects meet safety standards, regulatory compliance, and quality benchmarks, reducing costly errors and delays.
- Ineffective standardization practices, a large volume of complex documentation, and evolving compliance regulations make quality management challenging.
- Implementing QA/QC construction software can tackle these challenges by automating inspections, simplifying reporting, and ensuring real-time compliance.
In the construction industry, quality assurance (QA) and quality control (QC) are not just best practices—they are essential for minimizing errors, reducing costs, and ensuring project success.
According to the landmark Egan Report, 30% of all construction work involves rework. This rework, often caused by poor quality, can lead to a 300% loss in crew productivity (EC&M), resulting in significant delays and financial setbacks. Moreover, the Cost of Quality (CoQ)—which includes prevention, appraisal, and failure costs—can account for 5-6% of a project’s total budget, with costs rising sharply if quality issues are not addressed early.
By implementing robust QA and QC processes, construction companies can improve efficiency, reduce safety risks, and maintain compliance, ultimately ensuring better project outcomes.
- Quality Management in Building Construction
- Importance of Quality Control and Quality Assurance in the Construction Industry
- Key Components of Quality Assurance in Building Construction
- Essential Elements of Quality Control in Construction
- Challenges in QA and QC in Construction
- How a Construction QA/QC Software Can Help
- Streamline Construction Quality Management With GoAudits
Quality Management in Building Construction
Project quality management in construction encompasses all aspects of planning, execution, and evaluation to deliver safe, cost-effective, and high-performing structures.
Quality Control in Construction
Quality control (QC) in construction refers to the systematic process of inspecting, testing, and verifying that materials, procedures, and finished work meet specified quality standards. It involves comparing actual performance with required standards and taking action when a difference exists. This happens throughout the project lifecycle, from material procurement to final structure completion.
The fundamental goal is to identify and correct defects or deviations before they become major problems or reach the client. Although reactive in nature, effective quality control in construction projects significantly reduces the likelihood of defects reaching the completed structure.
Quality Assurance in Construction
Construction quality assurance (QA) encompasses the planned and systematic activities implemented within a quality system to provide confidence that a project will fulfill its quality requirements. Unlike QC, which focuses on detecting defects, construction quality assurance aims to prevent defects from occurring in the first place.
Construction QA is proactive, focusing on the processes, SOPs, and systems that will lead to quality outcomes. It establishes the framework within which QC activities operate. When implemented effectively, QA reduces the need for extensive quality control activities by ensuring that work is done correctly from the beginning.
Importance of Quality Control and Quality Assurance in the Construction Industry
Construction projects involve significant financial investment, complex coordination among multiple parties, and structures that must withstand decades of use. Without robust QA and QC, projects risk structural failures, safety hazards, cost overruns, and litigation. Quality management safeguards against these risks while enhancing reputation and profitability.
High-quality construction delivers buildings that perform as intended, with systems that function properly and materials that maintain their integrity over time. This translates to fewer warranty claims, reduced maintenance costs, and greater client satisfaction.
Furthermore, consistent quality practices improve operational efficiency by reducing rework, minimizing waste, and optimizing resource utilization. In an industry where safety is paramount, quality management plays a crucial role in preventing accidents and ensuring occupant safety.
Key Components of Quality Assurance in Building Construction
Here are the key components of quality assurance in the construction industry:
1. Developing a Quality Management Plan for Construction Projects
A comprehensive quality management plan is the foundation for all quality control activities in construction. This strategic document establishes the framework for achieving objectives while providing clear direction for all stakeholders.
- Setting Quality Objectives and Standards: The plan must align with project requirements, regulatory codes, industry standards, and client expectations. These objectives should be specific, measurable, achievable, relevant, and time-bound.
- Establishing Processes and Procedures: This involves developing systematic approaches for all quality-critical activities, which includes detailed work instructions that define how tasks should be performed, inspection procedures, and testing protocols.
- Assigning Roles and Responsibilities: This includes identifying who has authority to approve work, who conducts construction inspections, who manages non-conformances, and who maintains documentation.
2. Implementing a Construction Quality Assurance Plan
Effective implementation transforms quality planning into practical actions that protect project outcomes. This requires consistent application of quality principles across all project phases and participants.
- Regular Audits and Construction Quality Inspections form the verification backbone of any quality assurance system. Audits evaluate processes to ensure they remain effective and are being followed as designed. Inspections occur at predetermined stages, particularly before critical work is concealed by subsequent activities.
- Training and Competency Assessments: Ensure that all personnel understand quality requirements and possess the skills to execute work correctly. This includes orientation training that introduces the project’s quality objectives, technical training for specialized work, and ongoing refresher training to reinforce quality principles.
- Documentation and Record-keeping: Provide evidence that quality requirements have been met and create a traceable history of the project.
Construction Inspection Software: Learn how a construction inspection and quality control software helps track inspection data and quality metrics.
3. Construction Quality Management for Contractors
Contractors bear significant responsibility for quality outcomes. Their management approach must address both their direct activities and those performed by others under their direction.
- Ensuring subcontractor compliance requires contractors to extend their QMS to all subcontracted work. This begins during subcontractor selection, where quality capabilities should be evaluated alongside pricing and experience, and includes proactive oversight through pre-work meetings, progress reviews, and supplier inspections.
- Managing supplier quality involves controlling the materials and equipment that become part of the permanent structure. This includes qualifying suppliers, developing clear material specifications, implementing receiving inspection protocols, and maintaining traceability of critical materials.
- Continuous improvement initiatives recognize that quality management is not static but evolves throughout the project and from one project to the next. This involves analyzing quality data to identify trends and recurring issues, conducting root cause analysis, implementing corrective actions, and capturing lessons learned to prevent similar issues in the future.
Contractor Management Checklist: Use this template to ensure contractors adhere to safety and quality standards with inspections of site assessments, contracts, etc.
Essential Elements of Quality Control in Construction
The following are the essential elements of quality control during construction:
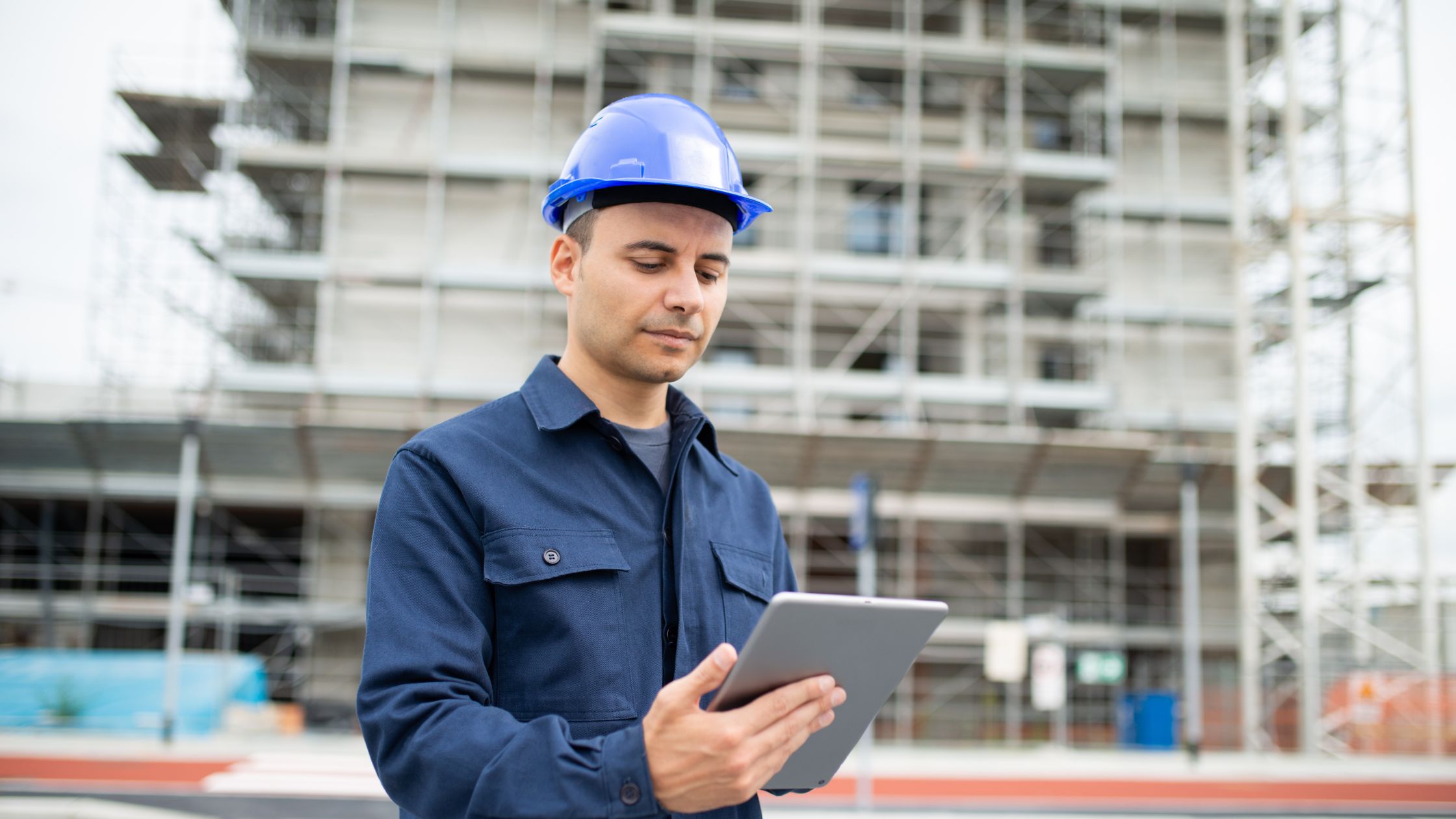
1. Building Construction Quality Control Plans
Quality control plans translate broader quality management objectives into specific verification activities. These tactical plans focus on the “what, how, when, and who” of quality verification.
- Defining inspection and test plans (ITPs) involves identifying all verification activities required for each work element. They typically include hold points where work must stop for mandatory inspection, witness points where inspection is available but not mandatory, and monitoring points where ongoing surveillance occurs.
- Establishing acceptance criteria provides clear, objective standards for determining whether work is acceptable. These criteria must be specific and measurable, leaving minimal room for subjective interpretation.
- Scheduling quality control activities must integrate with the construction sequence, recognizing dependencies between work elements and accommodating the time required for testing and reporting. The scheduling system must also allocate resources appropriately, preventing bottlenecks that could delay construction or compromise verification thoroughness.
Inspection and Quality Control App: Learn how businesses leverage GoAudits QC software to schedule and perform efficient quality inspections.
2. Quality Control Procedures in Construction
Quality control procedures provide step-by-step guidance for verification activities, ensuring consistency and thoroughness in quality evaluations.
- Material inspections and testing verify that construction materials meet specified requirements before and during incorporation into the work. This includes preliminary testing of proposed materials, verification of certifications and mill test reports, field sampling to confirm material properties remain consistent, and in-place testing to verify installed properties.
- Workmanship assessments evaluate installation quality through visual inspection, dimensional verification, and functional testing.
- Non-conformance reporting and corrective actions address work that fails to meet requirements, defining how deficiencies are identified, documented, and corrected.
Construction Building Quality Control Checklist: Here’s our free digital customizable QC template to help you get started.
3. Construction Site Quality Control Measures
Site-based quality control in construction projects addresses the unique challenges of the environment, where changing conditions and multiple trades interact in ways that can impact quality outcomes.
- On-site supervision and monitoring provide continuous quality oversight during work execution. This includes pre-activity meetings that review quality requirements before work begins, observation during execution to identify and correct improper methods, and post-activity reviews that document lessons learned.
- Safety and compliance checks ensure that work not only meets quality standards but also adheres to regulatory requirements and construction safety practices. While distinct from product quality, safety and compliance directly impact project success and often overlap with quality concerns. For example, improper fall protection might indicate a general disregard for standards that could extend to quality practices.
- Final inspections and handover processes represent the culmination of quality control efforts. These include punch list inspections, snagging, systems testing, and documentation review.
👉 Useful Resource: Free Construction Site Checklists
Use the following checklists to assess the quality control measures at construction project sites:
→ Construction Site Safety Checklists
→ Construction Site Risk Assessment Checklist
→ Construction Site Inspection Checklist
→ Construction Project Handover Checklist
→ Construction Punch List Template
» Use These Checklists: Sign up with our 14-day free trial to have these checklists customized.
Challenges in QA and QC in Construction
Here are the key challenges of implementing quality control and quality assurance in construction:
- Lack of Standardization: This challenge manifests in varying interpretations of requirements among project participants, inconsistent inspection criteria applied by different quality personnel, and incompatible quality systems among organizations working on the same project.
- Inconsistent Communication leads to misunderstandings about quality requirements and verification results. This includes incomplete distribution of updated documents, leading to work based on outdated requirements; delayed notification of non-conformances, allowing defective work to continue; and ineffective explanation of technical requirements to field personnel.
- Inadequate Documentation and QA/QC Reporting: Common challenges include incomplete records that fail to capture all required verification evidence, disorganized filing systems that make information retrieval difficult, and insufficient detail in non-conformance reports that hinder root cause analysis.
How a Construction QA/QC Software Can Help
QC software offers various features that help businesses move away from paper-based methods and adopt more efficient tech-driven QA/QC procedures in construction. Consider the following case study:
👉 How Woodside Homes Overcame the Challenges of Construction QC
Woodside Homes, a leading homebuilding company in the US, offers various solutions, including fully equipped and personalized housing. However, due to a lack of a formalized and systematic approach, the team found it challenging to inspect critical checkpoints and communicate the identified issues with trade partners, impacting the overall quality control.
The company adopted GoAudits construction inspection software to streamline its property quality control process. Custom digital checklists, an intuitive app, and automated reports helped teams enhance coordination with trade partners, improve overall quality, and simplify the general superintendent’s role, leading to significant efficiencies and time savings.
» Read More: How Woodside Homes streamline property inspections and quality control with GoAudits.
Let’s look at how a construction QC software helps tackle the challenges of QMS in the construction industry.
Digital Checklists for Standardization
Construction QA/QC software provides template libraries of standard digital checklists that can be customized to project-specific requirements while maintaining core verification elements.
For example, a concrete placement checklist would include standard items like formwork inspection, reinforcement verification, and pre-placement approval while allowing customization for project-specific mix designs.
Digital construction inspection checklists eliminate interpretation variations by providing clear acceptance criteria for each inspection point. This ensures that all inspectors apply the same standards regardless of experience level or background.
The construction QA software maintains checklist version control to ensure all team members can access the most current requirements. When specifications change, updates propagate immediately to all users, eliminating the risk of outdated checklists and construction SOPs continuing to circulate. The system also tracks which version was used for each inspection, creating an audit trail that demonstrates compliance with requirements in effect at the time of work.
User Defined Workflows and Communication Channels
Construction QA/QC software structures information flow and ensures critical quality information reaches the right people at the right time. User-defined workflows create standardized processes for quality activities while accommodating project-specific organizational structures.
The workflow feature allows managers to map out quality processes as sequential steps with clear responsibilities and timelines. For example, a non-conformance workflow might begin with initial identification, route to the appropriate supervisor for verification, proceed to the design team for disposition, and finally assign corrective actions to responsible parties.
Real-time notifications accelerate response to quality issues, reducing the impact of deficiencies. When an inspector identifies a non-conformance, the system immediately alerts responsible parties, allowing quick containment before the issue affects subsequent work.
Instant Reporting and Cloud Storage
Building QA/QC software automates construction quality control reporting and centralizes quality records in secure, accessible cloud storage. This approach transforms quality documentation from a burdensome administrative task to a valuable resource for project management and continuous improvement.
As soon as an inspector completes a checklist using the construction QC mobile app, the system automatically produces a formatted report with all verification results, notes, supporting evidence such as photos and notes, and the inspector’s signature. Custom report templates can be configured to match specific project or client requirements.
Cloud storage creates a centralized repository for all quality records, eliminating the fragmentation of paper files and local digital storage. Moreover, filtering features transform quality records from static archives to actionable intelligence. Users can quickly locate specific information based on location, date, inspection type, or status, eliminating the time-consuming manual search through paper files or disorganized digital folders.
Streamline Construction Quality Management With GoAudits
GoAudits is a construction quality control and inspection software that allows contractors to do their best work while meeting the safest and highest quality standards. Its scalable features allow builders to streamline processes, eliminate communication bottlenecks, enhance resource utilization, and handle multiple projects.
With GoAudits, you can:
- Create custom construction site inspection checklists.
- Schedule all types of construction inspections.
- Perform quality inspections using the GoAudits mobile app, even in locations with limited internet connectivity.
- Assign corrective actions and ensure their on-time completion.
- Make sure all stakeholders stay updated through instant reporting.
- Monitor adherence to all safety, quality, and operational standards.
With a rating of 4.8 stars on Capterra, GoAudits is trusted by some of the biggest names in the construction management industry.
» GoAudits Reviews: Read how companies leverage GoAudits to meet standards in their construction operations.