Workplace safety is a top priority in any industry, and ensuring proper protection starts with proactive inspections and risk assessments. Whether you operate in construction, manufacturing, healthcare, or any other field with potential hazards, understanding risks and ensuring the effectiveness of personal protective equipment (PPE) is essential. Regular PPE inspections help identify dangers before they lead to injuries, ensuring compliance with safety standards and protecting workers from harm.
This article will explore the key aspects that make PPE inspections indispensable for workplace safety.
- Types of PPE Hazards and Associated Risks
- What is a PPE Inspection?
- How to Conduct PPE Hazard Assessments?
- PPE Inspection Plan: Key Components
- When and How Often Should PPE Be Inspected?
- How to Conduct PPE Inspections?
- Streamline PPE Inspections with Safety Inspection Software
- OSHA PPE Hazard Assessment Requirements
- Do PPE Risk Assessments & Inspections Vary by Industry & Tasks?
- Best Practices for Proper PPE Use and Maintenance
Types of PPE Hazards and Associated Risks
PPE protects against workplace hazards like chemical, physical, electrical, and mechanical risks. However, improper selection or use can create new dangers. Identifying different types of hazards and their associated risks ensures effective protection and workplace safety.
- Inadequate or Improper PPE Selection: Selecting PPE that doesn’t align with specific workplace hazards can leave workers vulnerable. For instance, using gloves that are not resistant to particular chemicals can result in skin absorption of harmful substances.
- Poorly Fitting or Defective PPE: Ill-fitting PPE can compromise protection and hinder performance. Loose gloves may impair dexterity, while tight respirators might not seal correctly, exposing workers to airborne contaminants.
- Contamination and Hygiene Issues: Contaminated PPE can become a source of exposure. For example, reusable equipment not adequately cleaned can harbor hazardous substances, leading to skin conditions or other health issues.
- Restricted Mobility and Visibility: Some PPE can limit movement or obstruct vision, increasing the risk of accidents. Bulky suits or fogged goggles might lead to slips, trips, or falls.
- Heat Stress and Fatigue: Wearing PPE, especially in hot environments, can elevate body temperature, leading to heat stress. This condition can cause fatigue, dizziness, or heat-related illnesses.
- Communication Barriers: Certain PPE, like respirators or earmuffs, can hinder communication, leading to misunderstandings or accidents.
- Psychological and Behavioral Risks: Extended PPE use can cause discomfort, anxiety, or reduced job satisfaction. These psychological stresses might lead to decreased compliance or errors.
- Electrical and Static Risks: Some PPE materials can accumulate static electricity, posing ignition hazards in flammable environments.
- Reduced Sensory Perception: PPE like thick gloves or full-face masks can dull senses, affecting the ability to detect hazards.
- Failure to Maintain PPE: Neglecting regular maintenance can render PPE ineffective. Damaged or worn-out equipment may fail to provide necessary protection.
What is a PPE Inspection?
A PPE inspection is a thorough assessment of protective equipment to identify any issues, defects, damages, or wear and tear that could compromise its protective capabilities. It involves systematically examining PPE to ensure its effectiveness in safeguarding individuals against workplace hazards, and whether PPE meets safety standards.
The main objectives of PPE inspections are to:
- Verify that PPE functions properly and safeguards users from hazards
- Detect and resolve issues early to prevent failures and reduce costs
- Ensure compliance with occupational safety regulations and standards
PPE inspections can be performed by:
- Employees: Conduct pre-use inspections daily to detect obvious issues.
- Supervisors or Safety Officers: Carry out regular, detailed inspections, typically on a monthly basis, to ensure comprehensive safety compliance.
How are PPE Inspections Different from PPE Hazard Assessments & Risk Assessments?
PPE hazard assessments systematically identify potential workplace hazards that necessitate the use of PPE. It involves evaluating tasks and environments to determine if hazards such as chemical exposures, physical dangers, or biological risks are present or likely to be present. The primary goal is to select appropriate PPE to mitigate identified hazards.
PPE risk assessments dive deeper into analyzing the likelihood and severity of identified hazards. It evaluates the probability of hazard occurrence and the potential impact on employee health and safety. Quantifying risks helps employers prioritize hazard control measures before resorting to PPE. This aligns with the hierarchy of controls, emphasizing hazard elimination or substitution over mere protection.
Aspect | PPE Hazard Assessment | PPE Risk Assessment | PPE Inspection |
Objective | Identify workplace hazards requiring PPE | Analyze the likelihood and severity of identified hazards | Ensure PPE is in good condition and functioning properly |
Focus | Task and environmental hazards | Risk probability and impact | PPE wear, damage, and effectiveness |
Timing | Conducted before tasks begin | Conducted before tasks begin, with ongoing monitoring | Performed before and after each use, with periodic detailed checks |
Outcome | Determines the need for PPE and selection of appropriate gear | Helps prioritize control measures based on risk level | Identifies PPE defects, wear, and necessary replacements |
Benefits of Regular PPE Hazard & Risk Assessments
A thorough PPE hazard and risk assessment helps identify potential risks, such as falling objects, harmful chemicals, dust accumulation, and radiation exposure. Evaluating hazards and risks can help implement effective control measures and select appropriate PPE to minimize risks.
Properly maintained PPE, selected based on risk assessments, significantly reduces the likelihood of injuries. A safe work environment enhances employee confidence, morale, and productivity, fostering a culture of safety and accountability.
While regular PPE risk assessments require time and resources, they can lead to significant cost savings and productivity boosting in the long run. Organizations can avoid costly medical expenses, legal fees, and downtime associated with workplace incidents. Maintaining PPE in good condition extends its lifespan, reducing the need for frequent replacements.
An finally, regular PPE risk assessments and inspections are also essential for compliance with occupational safety regulations:
- Occupational Safety and Health Administration (OSHA): Sets and enforces standards across various industries to ensure safe working conditions.
- American National Standards Institute (ANSI): Develops consensus standards for PPE design and performance.
- National Fire Protection Association (NFPA): Provides guidelines for fire safety, including PPE requirements for fire-related hazards.
- Industry-specific agencies also play crucial roles:
- Food and Drug Administration (FDA): Regulates PPE in healthcare to ensure protection against biological hazards.
- Mine Safety and Health Administration (MSHA): Oversees safety protocols in mining, including appropriate PPE usage.
Adhering to these regulations not only ensures legal compliance but also demonstrates a commitment to employee safety.
How to Conduct PPE Hazard Assessments?
Follow the steps to conduct an effective PPE hazard assessment:
1. Identify Workplace Hazards
Walk through the worksite and examine tasks, equipment, and processes. Identify potential hazards in the following categories:
- Physical Hazards: Impact, vibration, sharp objects, extreme temperatures
- Chemical Hazards: Liquids, fumes, gases, dust, mists
- Biological Hazards: Bacteria, viruses, bloodborne pathogens
- Radiation Hazards: Ultraviolet, infrared, ionizing radiation
- Ergonomic Hazards: Repetitive motions, awkward postures, forceful exertions
👉 Use this free PPE hazard assessment template to identify workplace hazards, assess risks, and determine the PPE required.
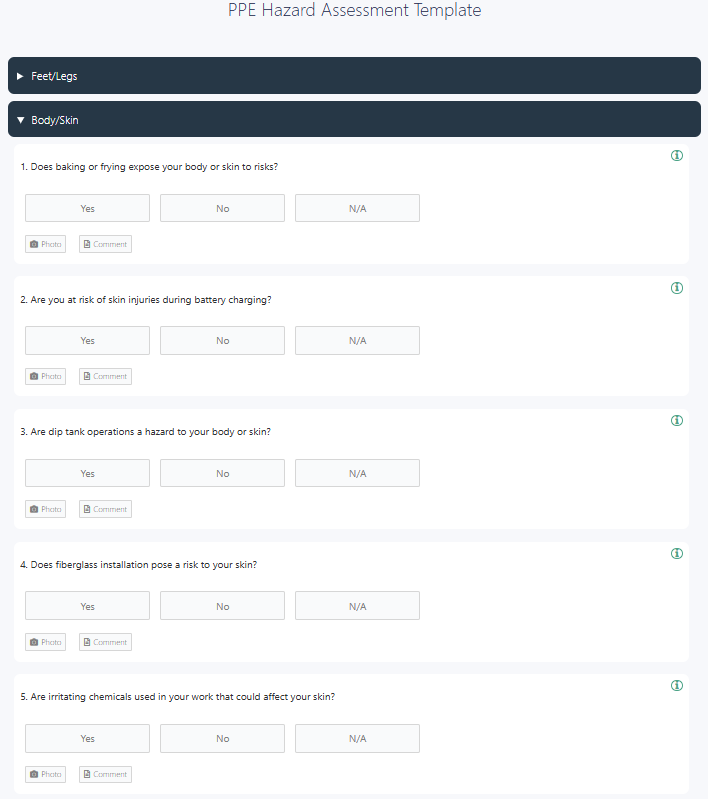
2. Evaluate Risks
Assess the likelihood and severity of each hazard. Consider:
- Frequency and duration of exposure
- Potential consequences of exposure
- Effectiveness of existing controls
3. Determine the Necessary PPE
Select appropriate PPE based on identified hazards. Below is an overview of different types of PPE:
- Eye and Face Protection: Protective devices such as safety glasses, goggles, and face shields offer comprehensive coverage against hazards like flying debris, chemical splashes, and harmful radiation.
- Respiratory Protection: Essential in environments with airborne contaminants, including dust, fumes, or hazardous gases, they range from particulate respirators, like N95 masks that filter out airborne particles, to more advanced devices such as self-contained breathing apparatuses (SCBAs) that supply clean air from an independent source.
- Skin and Body Protection: PPE such as gloves, lab coats, and face shields act as barriers between the skin and common hazards, including chemical agents, physical agents like extreme temperatures, mechanical trauma, and biological agents. Coveralls, aprons, and flame-resistant clothing provide additional protection in high-risk environments.
- Hearing Protection: PPE for hearing protection includes earplugs and earmuffs, which are essential in environments with potentially damaging noise levels.
- Head Protection: Safety helmets or hard hats are designed to protect the head from impact injuries caused by falling objects or bumping into hazards in construction, mining, and other industrial settings.
- Foot Protection: Safety footwear, including steel-toed boots and shoes with slip-resistant soles, protects against foot injuries from falling objects, punctures, or slips.
- Hand Protection: Gloves are vital for protecting hands from various hazards, including chemicals, cuts, and extreme temperatures.
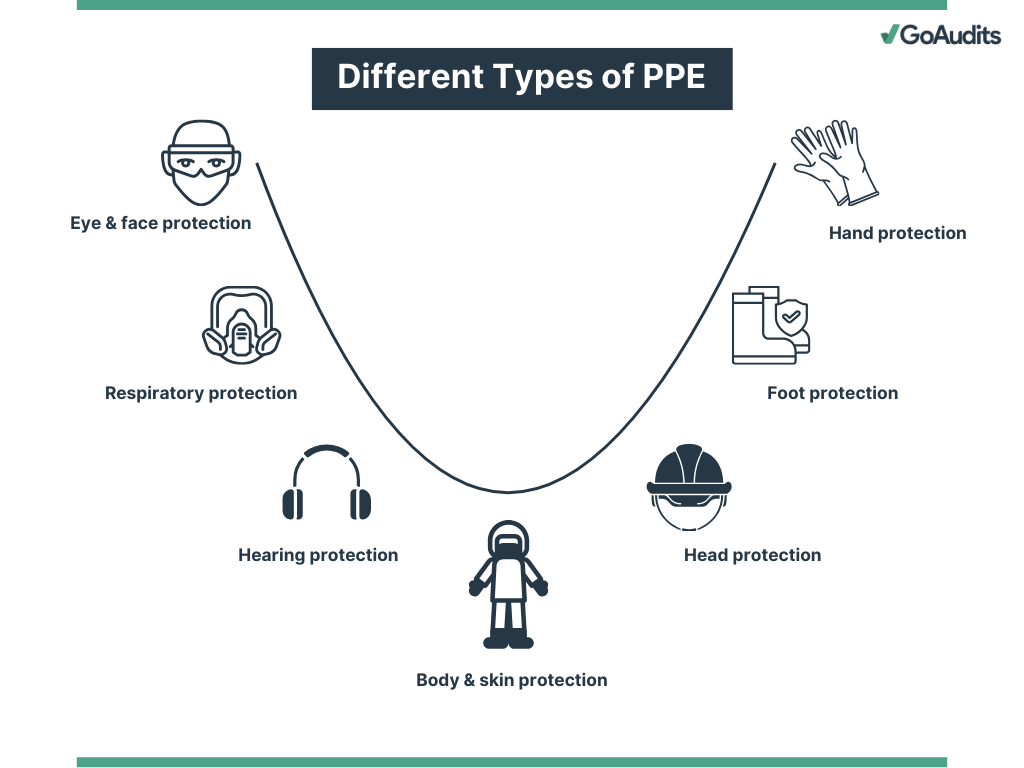
4. Implement PPE Use
Ensure workers have access to proper PPE. Conduct training on:
- Proper use and maintenance
- Limitations of PPE
- Correct storage and disposal
5. Document Findings
Create a written PPE hazard assessment report. Include:
- Identified hazards
- PPE recommendations
- Justifications for PPE selection
- Date and responsible personnel
6. Review and Update Regularly
Conduct periodic reassessments, especially after:
- Workplace modifications
- New equipment introduction
- Incident reports
👉 The steps for conducting PPE risk assessments and PPE hazard assessments are largely similar but differ in focus.
PPE hazard assessments involve identifying workplace hazards, assessing exposure levels, determining necessary PPE, documenting findings, and reviewing them regularly. PPE risk assessments go further by evaluating the likelihood and severity of harm using a risk matrix, assessing the effectiveness of current control measures, selecting appropriate PPE based on risk levels, and evaluating residual risks even after PPE is assigned.
A hazard assessment is a precursor to a risk assessment, and both are essential for workplace safety.
PPE Inspection Plan: Key Components
What is a PPE Inspection Plan?
A PPE inspection plan is a systematic, structured approach to ensure that all PPE used in the workplace is in optimal condition and provides the intended protection against hazards. It outlines procedures for regular inspections, maintenance, and replacement of PPE to safeguard employees’ health and safety.
A PPE inspection plan is important because it:
- Standardizes inspections to ensure PPE is checked consistently and thoroughly.
- Defines roles and responsibilities so inspections are conducted on time and correctly.
- Shifts PPE checks from a reactive task to a proactive, preventive measure.
- Ensures compliance with safety regulations and provides documentation for audits.
- Maintains detailed records to track PPE conditions, failures, and trends.
- Optimizes PPE maintenance and replacement, preventing unnecessary risks and costs.
- Reinforces a strong safety culture by making PPE inspections a structured routine.
Key Components of a PPE Inspection Plan
Here are the key components of PPE inspection plans.
- Scope and Objectives: Define the purpose of the PPE Inspection Plan. This includes identifying which types of PPE require inspections, the frequency of inspections, and the regulatory requirements that must be met.
- Roles and Responsibilities: Specify who is responsible for conducting inspections, maintaining records, and ensuring compliance. This typically includes safety officers, supervisors, and employees using the equipment.
- Inspection Procedures and Criteria: Establish standard procedures for PPE inspections. Define what should be checked for each type of PPE (e.g., helmets, gloves, eye protection) and the acceptable condition criteria.
- Frequency of Inspections: Determine how often inspections should occur – daily, weekly, monthly, or annually – based on PPE type, industry standards, and manufacturer recommendations.
- Reporting and Record-Keeping: Develop a system for logging inspection results, tracking deficiencies, and documenting corrective actions. This ensures compliance with regulations and helps identify recurring issues.
- Corrective Actions and PPE Replacement: Outline the process for addressing defective PPE, including how to report, repair, or replace equipment that fails an inspection.
- Compliance with Safety Regulations: Ensure alignment with Occupational Safety and Health Administration (OSHA) or other relevant safety standards to avoid violations and maintain a safe workplace.
- Employee Training and Awareness: Provide training for employees on how to inspect their PPE, recognize defects, and report issues. This reinforces accountability and proactive safety measures.
👉 A well-structured PPE inspection plan should align with your organization’s PPE SOPs to ensure consistency and compliance.
When and How Often Should PPE Be Inspected?
Here’s a complete breakdown of when and how often you should perform PPE checks.
- Inspection Before and After Each Use
Before each use, perform a visual and functional check of your PPE to identify any signs of damage, such as cracks, tears, or frayed straps. For instance, inspecting hard hats for cracks, safety glasses for scratches, and gloves for tears ensures that equipment performs as intended.
After use, re-examine the equipment to ensure it remains in good condition. It helps in the early detection of issues that could compromise safety.
- Regular Scheduled Inspections
In addition to pre-use checks, implement regular, scheduled PPE checks based on the type of equipment, frequency of use, and environmental conditions. These checks should be more detailed and conducted by experienced personnel. Though the frequency may vary, some equipment might require monthly inspections, while others could need quarterly reviews.
- Inspection After an Incident
After any incident involving PPE, such as exposure to hazardous substances, impacts, or accidents, perform an immediate and comprehensive inspection. This PPE assessment ensures that the equipment has not been compromised and remains capable of providing the necessary protection. If any damage or degradation is detected, promptly remove the PPE from service and replace it as needed.
Factors Influencing PPE Inspection Frequency
The frequency of PPE inspections depends on several key factors:
- Type of PPE
Different PPE items have varying inspection needs. For instance, safety harnesses require more frequent checks compared to hard hats. OSHA recommends inspecting PPE before each use, especially for equipment like safety harnesses, which have specific inspection requirements.
- Workplace Hazards
The nature of workplace hazards significantly influences PPE inspection frequency. Environments with exposure to chemicals, extreme temperatures, or physical threats necessitate more frequent PPE inspections to ensure ongoing protection.
- Frequency of Use
PPE used regularly undergoes more wear and tear, requiring more frequent inspections. Monitoring usage patterns helps predict the expected lifespan of the equipment.
- Manufacturer Guidelines
Manufacturers provide specific recommendations for PPE inspection intervals. Adhering to these guidelines ensures compliance with safety standards and maintains the equipment’s integrity.
- Regulatory PPE Inspection Requirements
Compliance with regulatory standards, such as those set by OSHA, is essential. These regulations often dictate minimum inspection frequencies and handling procedures for various PPE types.
- Storage and Maintenance Conditions
Proper storage and maintenance significantly affect PPE longevity. Storing equipment in clean, dry places away from direct sunlight and extreme temperatures prevents premature degradation. Regular cleaning and maintenance, as well as following manufacturer guidelines, are also crucial.
- Incident or Equipment Failure
After any incident or equipment failure, immediate inspection of PPE is mandatory. For example, if a hard hat absorbs an impact, it should be replaced to ensure continued protection.
How to Conduct PPE Inspections?
A systematic approach to PPE inspections involves several key steps:
1. Understand Regulatory Requirements
Begin by familiarizing yourself with the relevant safety regulations and standards applicable to your industry. For instance, in the United States, OSHA provides guidelines on PPE usage and maintenance. Understanding these requirements ensures compliance and enhances workplace safety.
2. Develop a Digital PPE Assessment Checklist
Creating a digital PPE tailored to your organization’s specific PPE ensures consistency and thoroughness during inspections. Digital PPE risk assessment templates facilitate easy updates and accessibility, streamlining the inspection process.
👉 GoAudits offers a range of customizable PPE risk assessment templates. You can sign up for free and start using these PPE inspection checklists.
- PPE Hazard Assessment Template
- PPE Audit Checklist
- Daily PPE Inspection Checklist
- Donning and Doffing PPE Checklist
- Arc Flash PPE Suit Inspection Checklist
- Monthly PPE Inspection Checklist
- Confined Space PPE Checklist
- Security Guard PPE Checklist
- Firefighter PPE Inspection Checklist
- OSHA Personal Protective Equipment (PPE) Checklist
3. Perform Regular Inspections Before and After Use
Inspect PPE both before and after each use to identify any damage or wear that could compromise its effectiveness. Establish a routine inspection schedule based on the factors listed above to ensure reliability and compliance with safety standards. Regular PPE inspections help detect issues early, preventing potential injuries.
4. Evaluate Fit and Functionality
Ensure that PPE fits each employee properly and functions as intended. Ill-fitting equipment can reduce protection and may lead to discomfort or non-compliance.
5. Identify & Address Signs of Wear and Damage
Look for common signs of wear and damage, such as:
- Inspect helmets for cracks, dents, or other visible damage
- Check safety glasses or goggles for scratches, cracks, or loose parts
- Examine gloves for tears, punctures, or signs of degradation
- Assess boots for sole wear, holes, or compromised structural integrity
Promptly address any identified issues by repairing or replacing defective PPE. Using compromised equipment can lead to serious injuries and violate safety protocols.
6. Document Findings & Take Corrective Actions
Maintain detailed records of all inspections, noting any issues identified and corrective actions taken. Proper documentation ensures accountability and facilitates tracking of equipment maintenance.
7. Train Employees
Provide comprehensive training to employees on proper PPE usage, inspection procedures, and maintenance practices. Well-informed employees are more likely to adhere to safety protocols and report potential issues.
Streamline PPE Inspections with Safety Inspection Software
Managing PPE risk assessment is crucial for maintaining workplace safety and compliance. GoAudits safety inspection software is an all-in-one solution to simplify and streamline your PPE inspections, ensuring they are efficient and effective. Here’s how GoAudits helps you enhance accuracy, accountability, and overall safety compliance.
- Choose from an extensive library of health & safety checklists tailored specifically for PPE hazard assessments and inspections. You can customize these checklists, create your own, or let us do it for you.
- Conduct inspections up to 5 times faster using a smartphone, tablet, or computer, even without an internet connection.
- Upload and annotate photos, add e-signatures, and automatically record timestamps and geolocation data to ensure accountability and transparency.
- Automatically generate detailed, professional reports, including attached photos, assigned actions, and timestamps, after completion of each inspection. Customize these reports to reflect your brand and share them with relevant stakeholders.
- Assign corrective actions to specific team members, set priorities, and establish due dates.
- Track the completion status of tasks and receive notifications about overdue actions, helping to maintain high safety standards.
- Gain real-time insights into your PPE inspection performance. You can monitor audit scores across various locations, teams, or topics, and drill down from trend graphs to individual inspection reports.
- Identify patterns, recurring issues, and areas for improvement, facilitating data-driven decision-making to enhance workplace safety.
Free Health & Safety Audit Checklists for Workplaces
In addition to PPE risk assessment templates, GoAudits also offers a range of customizable health and safety audit checklists you can use to ensure overall workplace safety and compliance.
- Electrical Safety Inspection Checklist
- Risk Management Checklist Template
- OSHA Ladder Safety and Fall Protection Checklist
- Fire Safety Inspection Checklist
- Ergonomic Risk Assessment Template
- Chemical Safety Checklist – COSHH
- Office Hazards Checklist
- Confined Space Risk Assessment Form
- JSA Form – Job Safety Analysis Checklist
- Workplace Inspection Checklist
OSHA PPE Hazard Assessment Requirements
Ensuring workplace safety is a fundamental responsibility of employers, as mandated by OSHA. Conducting thorough hazard assessments to identify potential risks and implementing appropriate measures is an essential aspect.
- Workplace Hazard Evaluation
Workplace hazard evaluation is the initial step in safeguarding employees. It entails a detailed walkthrough of the facility to identify potential physical and health hazards. Physical hazards might include moving machinery, electrical sources, high temperatures, or sharp objects. Health hazards could involve exposure to harmful chemicals, dust, or radiation. These hazards should be properly documented to inform subsequent safety measures.
- Job Hazard Analysis (JHA)
To effectively identify and control hazards associated with specific job tasks, employers should perform a Job Hazard Analysis (JHA). It involves breaking down a job into its individual steps, evaluating each for potential hazards, and determining the necessary controls to mitigate identified risks. JHA contributes to safer work practices and enhances overall workplace safety.
- Hazard Assessment Certification
OSHA mandates that employers not only conduct hazard assessments but also verify their completion through written certification. This certification must identify the workplace evaluated, the person certifying the assessment, the date(s) of the assessment, and clearly label the document as a certification of hazard assessment.
- PPE Selection & Employee Training
Employers must select PPE that effectively protects against identified hazards. PPE should be properly designed, well-fitted, and communicated to employees. Additionally, employees must be trained on PPE usage, including when it is required, how to wear and maintain it, its limitations, and proper disposal.
- Periodic Reassessment
It is imperative for employers to periodically reassess the workplace to identify any new hazards that may arise. Regular reviews of injury and illness records can help spot trends or areas of concern, prompting appropriate corrective actions. This process ensures that safety measures, including the suitability and condition of existing PPE, remain effective and up-to-date.
Do PPE Risk Assessments & Inspections Vary by Industry & Tasks?
Yes, PPE hazard and risk assessments, as well as PPE inspections, vary significantly by industry and task due to unique work environments, potential risks and hazards, and regulatory requirements associated with different work environments and activities.
Variation in PPE Hazard and Risk Assessments
PPE hazard assessments are tailored to the specific risks present in a workplace or task.
Industry-Specific Risks
Each industry has distinct hazards that require tailored assessments. For example:
- Construction involves risks like falls from heights, heavy machinery accidents, and exposure to hazardous substances.
- Healthcare focuses on biological hazards, infection control, and patient safety.
- Oil and gas operations deal with high-risk environments like flammable materials and confined spaces.
Task-Specific Evaluations
Hazard assessments also vary by task within an industry. For instance:
- Plasma cutting in manufacturing requires PPE like flame-resistant gloves, welding helmets, and protective clothing due to the risks of burns and explosions.
- Confined space work necessitates respiratory protection and harnesses due to the risks of toxic gas exposure or falls.
Assessment Methods
Generic risk assessments apply to routine tasks across industries, while site-specific assessments address unique hazards at particular locations or tasks.
Variation in PPE Inspections
PPE inspections are equally diverse based on industry needs and task-specific requirements. Inspection techniques may involve systematic approaches (e.g., inspecting equipment from top to bottom) and sensory evaluations.
👉 The variability in PPE hazard assessments and inspections ensures that industries address their unique risks effectively. While general guidelines exist for conducting these evaluations, the specifics such as the type of PPE required or inspection intervals are highly dependent on the industry and the nature of tasks performed. A one-size-fits-all approach is ineffective due to varying risks and regulatory demands.
Best Practices for Proper PPE Use and Maintenance
Proper PPE use and maintenance prevents workplace injuries and ensures compliance with safety regulations. Follow these key steps:
- Select the Right PPE: Conduct a hazard assessment to determine the appropriate protective gear. Ensure proper fit for effectiveness and comfort.
- Train Employees: Educate staff on when and how to use PPE, including donning, doffing, limitations, and care.
- Inspect and Replace as Needed: Check PPE before each use and replace any damaged or expired equipment. Follow manufacturer guidelines for maintenance.
- Promote a Safety-First Culture: Lead by example, encourage compliance, and create an open environment for discussing safety concerns.