Did you know an estimated 600 million people, nearly 1 in 10 globally, fall ill after eating unsafe food? These cases result in approximately 420,000 deaths and a loss of 33 million healthy life years. Even the United States reports 43,000 deaths per year associated with unsafe consumer products. These figures highlight the importance of manufacturing standards that ensure products are safe for consumption, and that’s exactly what good manufacturing (GMP) principles are for. However, GMP principles are not limited to food manufacturing alone; they are also crucial for pharmaceuticals, cosmetics, and medical devices. GMP ensures that products are consistently produced and controlled according to quality benchmarks. Though the main goal is to minimize contamination risks and errors, the focus is not only on the final products but also on the entire manufacturing process from procurement to formulation and packaging.
This article will discuss the 10 GMP principles, their importance, and steps and free checklists to implement them.
What are GMP Principles?
GMP stands for Good Manufacturing Practice, a comprehensive framework for ensuring the consistent quality and safety of products in the manufacturing sector, particularly in industries like pharmaceuticals, food, cosmetics, and medical devices. GMP helps minimize the risks inherent in any production process that cannot be eliminated through testing the final product.
The 10 GMP principles cover all aspects of production, from the starting materials, premises, and equipment to the training and personal hygiene of staff. It also focuses on preventing contamination, mix-ups, and errors, helping manufacturers control their production processes more effectively.
The five pillars of GMP are essential for GMP audits and compliance and include the following:
– People
– Premises
– Processes
– Products
– Procedures
Learn More: How to Prepare for GMP Audits?
Why Should You Implement GMP Principles?
No matter the industry or your processes, the 10 GMP principles provide the essential guidelines to achieve
- Enhanced Product Quality and Safety: By implementing the 10 basic principles of GMP, manufacturers can ensure their products are consistently produced and controlled according to quality standards. This reduces risks related to contamination, errors, and inconsistencies in production processes.
- Improved Efficiency and Cost Savings: GMP helps in identifying and correcting inefficiencies in the production process, which can lead to cost savings. By optimizing operations and reducing waste, companies can achieve better resource management and lower production costs.
- Regulatory Compliance: Implementing the basic principles of GMP is a fundamental requirement for the legal manufacture and sale of pharmaceuticals and other regulated products. Non-compliance can result in fines, product recalls, and damage to a company’s reputation.
- Consumer Confidence: Quality assurance through GMP compliance builds consumer confidence in a brand. Knowing that a product is manufactured according to international quality standards assures customers of its safety and efficacy, leading to increased brand loyalty and market share.
- Market Expansion: GMP compliance is often a prerequisite for entering new markets, especially in the pharmaceutical and food industries. By complying with the ten principles of GMP, companies can expand their market reach to include international customers and markets that demand high-quality production practices.
What are the 10 GMP Principles?
Let’s dive into the 10 basic principles of GMP.
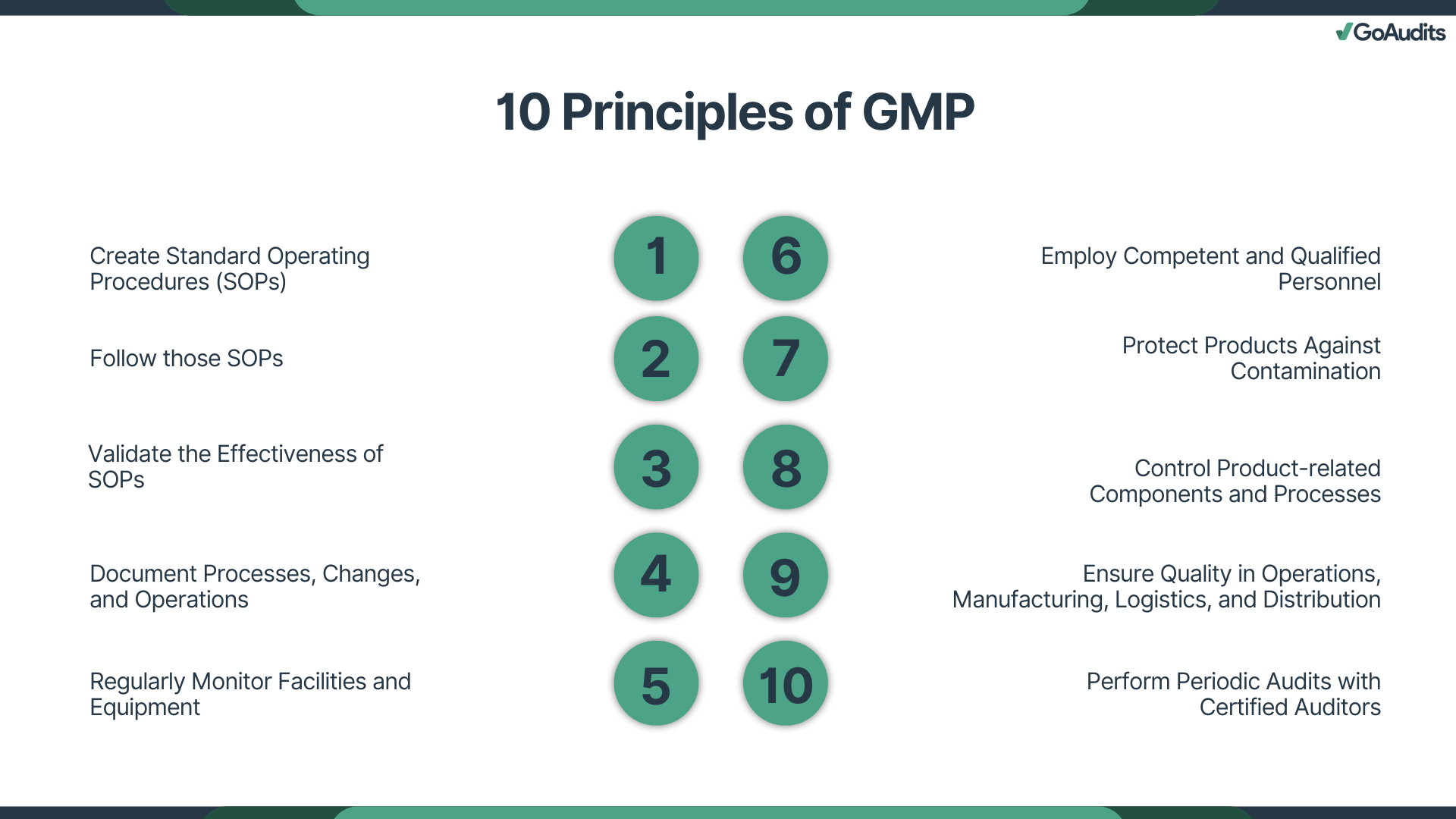
1. Create Standard Operating Procedures (SOPs)
The first of the 10 GMP principles is to create detailed, written SOPs for each process that could impact the quality of the final product. These SOPs will help streamline processes and ensure compliance with the desired quality standards.
2. Follow SOPs
Creating SOPs isn’t enough. Following these SOPs is important. Deviations from documented procedures can lead to quality issues, emphasizing the need for strict compliance.
3. Validate SOPs
Once these SOPs are followed, it’s important to validate their effectiveness in implementing the 10 basic principles of GMP. This involves creating evidence that the processes, techniques, and productions maintain the expected level of compliance at all stages.
4. Document Everything
Documentation is one of the basic principles of GMP. It involves keeping detailed records of processes, changes, and operations to ensure traceability and accountability.
5. Monitor Facilities and Equipment
Regular maintenance and monitoring of manufacturing facilities and equipment are essential to avoid contamination and ensure products are produced under the right conditions.
6. Employ Competent and Qualified Personnel
A well-trained and qualified workforce is one of the fundamental GMP principles. Continuous training and assessment ensure employees remain competent in their respective roles.
7. Protect Products Against Contamination
This GMP principle involves implementing stringent cleanliness and hygiene practices. These practices are essential to prevent product contamination and ensure consumer safety.
8. Control Product-Related Components and Processes
This GMP principle involves managing all aspects of production, ranging from raw materials to finished products, to prevent errors and ensure quality.
9. Ensure Quality in Operations, Manufacturing, Logistics, and Distribution
Quality control should be embedded in every phase of the production and distribution process to ensure the final product meets the required standards.
10. Perform Periodic Audits with Certified Auditors
Conducting regular audits is the last of the ten principles of GMP. Regular audits help verify compliance with GMP standards, identify areas for improvement, and ensure corrective actions are implemented effectively.
Implementing GMP Principles with GoAudits
Implementing the basic principles of GMP can be complex, but with the right tools, it becomes manageable and efficient. GoAudits is an all-in-one compliance software that offers a suite of features designed to support businesses in adhering to GMP principles effectively. Here’s how you can use GMP software:
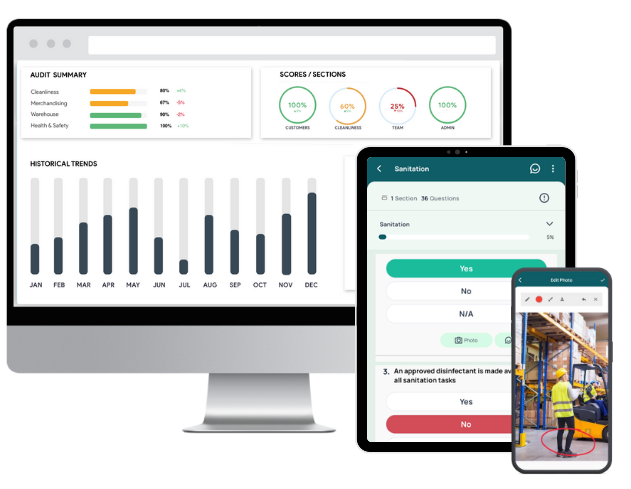
- GoAudits allows you to digitize SOPs, making them easily accessible to your team anytime, anywhere.
- You can perform regular audits using customizable checklists that reflect your specific SOPs, ensuring that every team member follows the same protocols consistently.
- GoAudits simplifies documentation with real-time data capture during audits. Every action, observation, and corrective measure is automatically documented, creating a comprehensive and date-stamped audit trail.
- The automated report generation feature further helps in maintaining detailed records that are essential for regulatory compliance and internal reviews.
- Schedule regular audits and inspections to ensure that your equipment is operating correctly and your facilities meet cleanliness standards.
- GoAudits mobile app enables on-the-spot reporting, which means issues like equipment malfunctions or facility lapses can be immediately recorded and addressed, preventing potential quality breaches.
- Use custom scoring systems to quantify audit outcomes, making it easier to track performance and identify areas needing improvement.
- Alerts and notifications ensure that any deviation from the set quality standards is quickly communicated, allowing for prompt corrective actions.
- GoAudits’ workflow management can help you set up efficient systems for logging complaints, initiating investigations, and executing recalls if necessary.
- GoAudits’ real-time analytics tool provides insights into audit data, helping you identify trends, anticipate potential issues, and implement improvements proactively.
Free GMP Audit Checklists
GoAudits offers a library of free GMP audit checklists tailored to various industries. You can use one of our GMP audit checklists below to get started, create your own checklist, or you can let us do it for you at no cost.
- GMP Self Inspection Checklist
- GMP (Good Manufacturing Practice) Audit
- GMP Inspection Checklist
- GMP Checklist for Breweries
You can also explore our library of free and customizable restaurant checklists and manufacturing audit checklists.
You can use these checklists to ensure your manufacturing facilities and products meet quality standards.
- ISO 9001:2015 Supplier Audit Checklist – Manufacturing
- Food Manufacturing Hygiene Audit
- Food Manufacturing SOP
- Manufacturing Process Audit Checklist
- Manufacturing Audit Checklist
- Food Safety & Hygiene Checklist
Principles of GMP in the Food Industry: Importance & Challenges
GMP for food manufacturing is designed to ensure that food products are consistently produced and controlled according to quality standards. The goal is to minimize the risks involved in food production that cannot be eliminated through testing the final product.
In the United States, the Food and Drug Administration (FDA) oversees GMP regulations, which are outlined in the Code of Federal Regulations (CFR).
Additionally, international standards such as ISO 22000 provide a framework for food safety management systems worldwide, focusing on the chain of food production and supply.
GMP Principles and HACCP Integration
Integrating GMP with Hazard Analysis Critical Control Point (HACCP) creates a robust food safety management system. GMP lays the groundwork by establishing the operational conditions needed for food safety, while HACCP provides a systematic approach to identify, evaluate, and control food safety hazards. This combination enhances food safety by addressing both the environment in which food is produced and the production process itself.
👉 Free Resources
GoAudits HACCP software offers a wide range of free HACCP checklists to simplify HACCP internal audits and self assessments. You can sign up for free and start using these checklists or you can digitize your HACCP-based SOPs.
→ Plan for HACCP
→ HACCP Audit Checklist
→ HACCP-Based SOPs
→ HACCP Plan Self-Assessment Checklist
→ HACCP Food Safety Checklist
→ HACCP Internal Audit Checklist
→ BRC Audit Checklist Food Safety Plan – HACCP (Clause 2)
Challenges in Implementing the 10 Principles of GMP in Food Industry
Food manufacturers face several obstacles in implementing the 10 principles of GMP in the food industry.
- Cost Implications: Implementing the GMP principles for the food industry can be costly, requiring investment in facility upgrades, employee training, and quality control systems.
- Complex Regulatory Compliance: Navigating the complex web of regulations and standards at both the national and international levels can be challenging.
- Maintaining Documentation: Comprehensive documentation of processes, procedures, and safety checks is critical but can be time-consuming and requires meticulous attention to detail.
- Cross-functional Coordination: Ensuring effective communication and coordination across different functions within the organization is essential for maintaining GMP principles in the food industry.
👉 Success Story: Nissin Foods USA
Nissin Foods, a renowned name in the food industry, faced delays due to its reliance on paperwork, making it challenging to collect data effectively. GoAudits enabled them to streamline their inspection processes, creating and managing standard operating procedures with ease. They were able to conduct more frequent and thorough audits, achieving a completion rate of 96% for GMP audits. GoAudits helped Nissin Foods ensure all aspects of production met the stringent quality standards expected in the food industry.
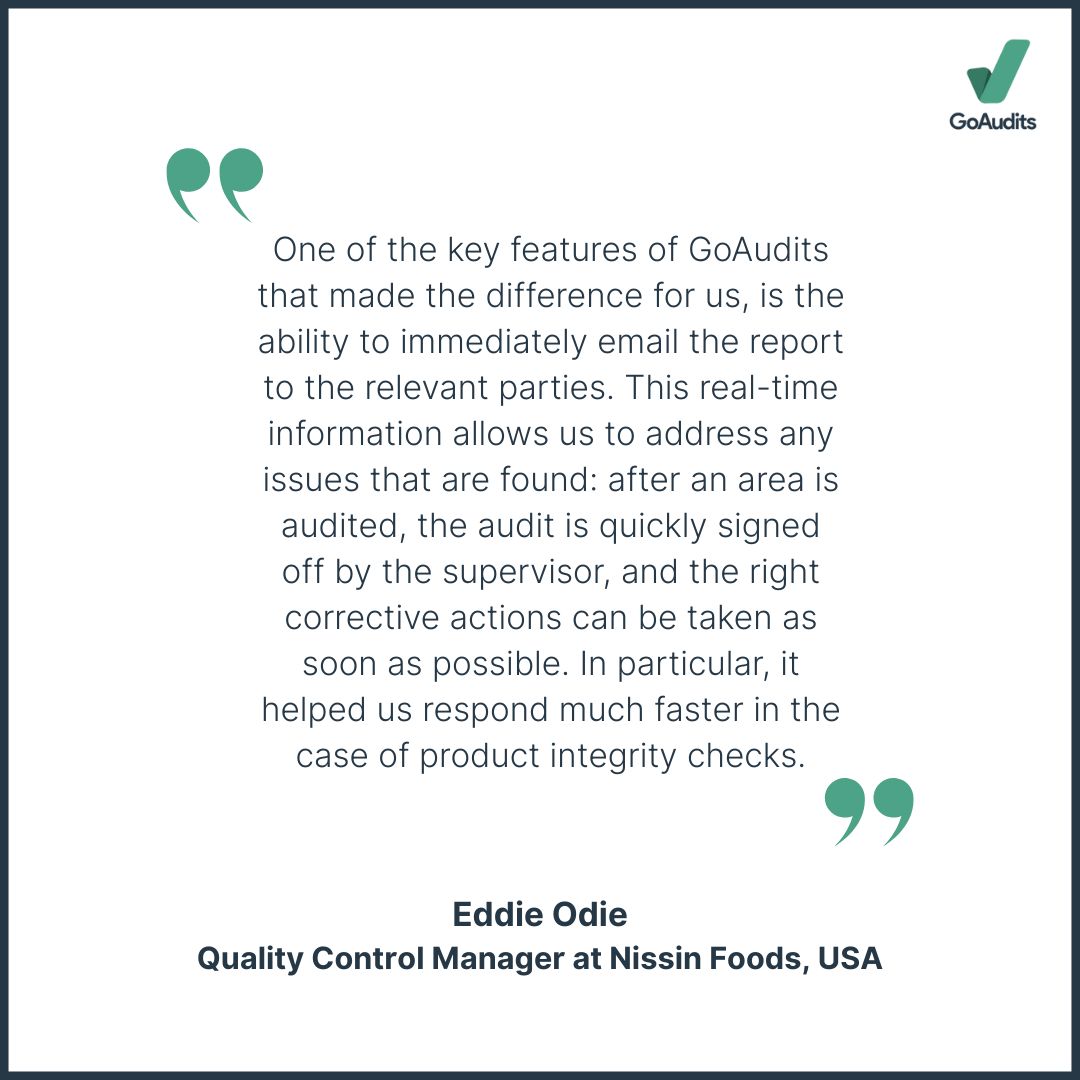
Implementing 10 GMP Principles: Challenges and Solutions
Let’s dive into some of the common challenges businesses face while implementing the 10 basic principles of GMP and how GoAudits can help overcome them.
- Navigating CAPA Management
Corrective action and preventive action (CAPA) management is a significant challenge in implementing the 10 GMP principles, focusing on investigating and rectifying discrepancies while preventing their recurrence.
CAPAs often originate from various situations like deviation investigations, out-of-specification investigations, and audit observations. A substantial portion of CAPAs even arises from simple errors, highlighting the importance of clear communication and documentation in the manufacturing process.
👉 GoAudits corrective action software streamlines CAPA management through its integrated workflow, where issues detected during audits can be immediately flagged for corrective or preventive actions. This enables organizations to track the lifecycle of a CAPA from initiation through to resolution, ensuring accountability and efficiency. Automated alerts and follow-up features ensure timely resolution of issues, directly supporting the CAPA process’s effectiveness.
- Managing Audits More Efficiently
GMP auditing challenges include developing or maintaining a program, measuring against regulations, and finding the time to audit. To manage these challenges, businesses can perform risk assessments on outsourced materials and services, define qualification processes for suppliers based on risk level, and perform confirmation testing of materials and components.
👉 GoAudits simplifies the development and execution of audit programs with its scheduling and planning features, ensuring audits are conducted timely and efficiently. It provides a comprehensive suite of reporting tools that allow organizations to measure their operations against regulatory standards and identify areas for improvement. The ability to customize audits and reports to specific regulatory requirements enhances the effectiveness of audit programs.
- Leveraging Document Management Systems
Implementing the ten principles of GMP heavily relies on robust documentation and recordkeeping. These practices are essential not only for ensuring product quality and safety but also for complying with regulatory standards such as those enforced by the FDA.
Challenges in documentation and recordkeeping arise from the need to accurately capture and maintain detailed records that are accessible, legible, and easily retrievable. The complexity increases with the involvement of various stakeholders like contractors and suppliers, making it crucial for every participant in the supply chain to adhere to these standards.
👉 GoAudits offers features that ensure all relevant documentation is accurately captured, securely stored, and easily retrievable. It supports GMP compliance by enabling digital signatures, maintaining a complete and auditable record of all documents, and ensuring that document review and approval processes are followed.