Do you find yourself overwhelmed by the complexity of your warehouse operations? What if you had a detailed roadmap that guides every operation, ensuring that tasks are performed efficiently, safely, and consistently? Warehouse standard operating procedures (SOPs) are essential documents for warehouse managers and employees to bring order and clarity to daily operations. This means fewer errors, faster turnaround times, and a more organized work environment. As for the staff directly working on the warehouse floor, warehouse SOPs eliminate guesswork and ensure uniformity in how each task is executed.
Let’s find out how warehouse SOPs streamline processes, improve safety, and ensure consistency across all operations in your warehouse.
What are Warehouse Standard Operating Procedures (SOPs)?
Warehouse Standard Operating Procedures (SOPs) are detailed instructions designed to ensure consistency and efficiency in performing routine tasks within a warehouse setting. These procedures play a crucial role in maintaining order, safety, and productivity across various industrial environments.
Warehouse SOPs are formalized guidelines that outline how specific operations should be carried out. They provide a step-by-step approach to tasks such as inventory management, order fulfillment, and safety checks, ensuring that every employee follows the same procedures. The primary purpose of these SOPs is to minimize errors, improve efficiency, and maintain consistently high-quality standards across all warehouse operations.
What are the Benefits of Warehouse Standard Operating Procedures?
Warehouse SOPs offer numerous benefits that enhance efficiency, safety, and overall operational effectiveness. Here are the key advantages:
- They streamline warehouse processes by providing clear, step-by-step instructions, reducing guesswork and minimizing workflow interruptions.
- By standardizing tasks, SOPs for warehouse operations ensure that all employees perform their tasks uniformly, leading to consistent results and dependable service delivery.
- Comprehensive warehouse SOPs include safety protocols that help prevent accidents and injuries.
- Well-documented procedures assist in meeting industry regulations and standards, simplifying audits and inspections.
- By minimizing errors and inefficiencies, warehouse SOPs contribute to cost savings through optimized resource utilization and decreased waste.
- Warehouse SOPs are valuable training tools, helping new employees understand their responsibilities and perform tasks correctly from the outset.
- SOPs for warehouse inventory management help maintain accurate stock levels, reduce discrepancies, and improve order fulfillment accuracy.
- Regularly reviewed and updated warehouse SOPs encourage ongoing assessment and refinement of warehouse processes, leading to continuous operational enhancements.
- They allow tasks to be delegated confidently, ensuring that operations continue smoothly even in the absence of key personnel.
- Consistent and efficient warehouse operations lead to timely and accurate order fulfillment, enhancing customer trust and satisfaction.
Types of Warehouse Standard Operating Procedures
Here, we’ll explore different types of warehouse SOPs, including those for inventory management, receiving, picking, packing, and dispatch, as well as overall warehouse operations.
SOP for Warehouse Inventory Management
Effective inventory management is the backbone of warehouse operations. An SOP for inventory management typically includes procedures for inventory tracking, stock audits, and maintaining accurate records. It outlines the methods for receiving, storing, and issuing inventory, ensuring that stock levels are optimized to meet demand without overstocking or understocking. The SOP for warehouse inventory management also covers procedures for handling discrepancies, managing returns, and conducting regular physical inventories to verify accuracy.
Warehouse Receiving SOP – Inbound
The warehouse receiving SOP focuses on the inbound process, detailing how to handle incoming shipments efficiently. This SOP includes steps for inspecting and verifying the received goods against purchase orders, documenting any discrepancies or damages, and updating the warehouse management system (WMS). The warehouse receiving SOP also outlines the proper procedures for unloading, unpacking, and storing items in designated locations within the warehouse.
👉 Use the GoAudits warehouse receiving checklist template to evaluate incoming goods, enhance accuracy, and ensure operational efficiency in your warehouse.
SOPs for Picking, Packing, and Dispatch – Outbound
The picking, packing, and dispatch SOPs are crucial for managing the outbound process in a warehouse. The SOP for receiving goods in a warehouse provides detailed instructions for order fulfillment, starting from picking items based on customer orders to packing them securely and dispatching them for delivery.
The warehouse picking SOP ensures that the correct items are selected and prepared for packing. The packing SOP includes guidelines for packaging materials, labeling, and quality checks to prevent shipping errors. Finally, the dispatch SOP outlines the steps for coordinating with logistics partners, generating shipping documentation, and updating the WMS to reflect the shipment status.
SOPs for Warehouse Operations
The SOP for warehouse operations includes a wide range of activities aimed at maintaining overall efficiency and safety. They cover areas such as waste control, quality assurance, and continuous improvement. They include procedures for maintaining cleanliness, ensuring safety protocols are followed, managing equipment and machinery, and conducting regular safety drills. Additionally, the SOP for warehouse operations often includes guidelines for handling emergencies, managing employee shifts, and ensuring compliance with legal and regulatory requirements.
What are the Steps to Develop and Implement Warehouse SOPs?
Here’s a step-by-step guide on effectively developing and implementing these procedures.
1. Identify Essential Warehouse Processes
Start by identifying the key processes in your warehouse. This includes receiving goods, inventory management, order picking, packing, shipping, and safety protocols. Understanding these processes helps ensure that your warehouse SOPs cover all critical areas, minimizing errors and improving efficiency.
2. Define the Scope and Objectives
Clearly define the scope and objectives of each warehouse SOP. Determine what each procedure aims to achieve and which specific processes it will cover. This ensures that your SOPs are focused and relevant, addressing the unique needs of your warehouse operations.
3. Gather Detailed Input from Warehouse Staff
Your warehouse staff are experts in daily operations. Gather detailed input from them to understand the nuances of each process. Conduct interviews, surveys, and brainstorming sessions to collect their insights and suggestions. It ensures that your warehouse SOPs are practical and comprehensive.
4. Draft Clear, Step-by-Step Instructions
When drafting your warehouse SOPs, clarity is key. Write step-by-step instructions that are easy to understand and follow. Use simple language and short sentences. Include detailed descriptions, diagrams, and checklists to enhance comprehension and reduce ambiguity.
Begin by identifying and prioritizing key processes that require standardization. Collaborate with team members who are directly involved in these tasks to gather accurate and practical insights. Choose an appropriate format, whether it’s step-by-step instructions, flowcharts, or checklists, and ensure it’s easy to follow. Document every step in detail, including necessary resources and any potential exceptions.
Incorporate visual aids to enhance understanding and keep the language clear and concise. Regularly review and update the warehouse SOPs to reflect any changes in procedures or regulations. Training your staff on these procedures and using digital tools for version control and accessibility can further streamline the implementation and compliance with warehouse SOPs.
5. Review and Test the SOPs
Before finalizing your warehouse SOPs, conduct thorough reviews and tests. Involve key stakeholders, including managers and warehouse staff, to review the procedures for accuracy and completeness. Pilot the warehouse SOPs in real-world scenarios to identify any gaps or issues and make necessary adjustments based on feedback.
6. Implement and Train Your Employees
Once the warehouse SOPs are finalized, implement them across your warehouse. Conduct comprehensive training sessions for all employees to ensure they understand and can effectively follow the new procedures. Provide hands-on training and create opportunities for employees to ask questions and clarify doubts.
7. Monitor and Continuously Improve
The implementation of warehouse SOPs is not a one-time task. Continuously monitor their effectiveness and gather feedback from warehouse staff. Regularly review and update the procedures to incorporate new technologies, regulatory changes, and operational improvements. This ongoing refinement ensures that your SOPs remain relevant and effective over time.
Leverage GoAudits for Warehouse SOP Management
GoAudits is a comprehensive solution for inspections, audits, quality control, and compliance. Here’s how you can use it to streamline your warehouse SOP management, ensuring your operations run smoothly and efficiently.
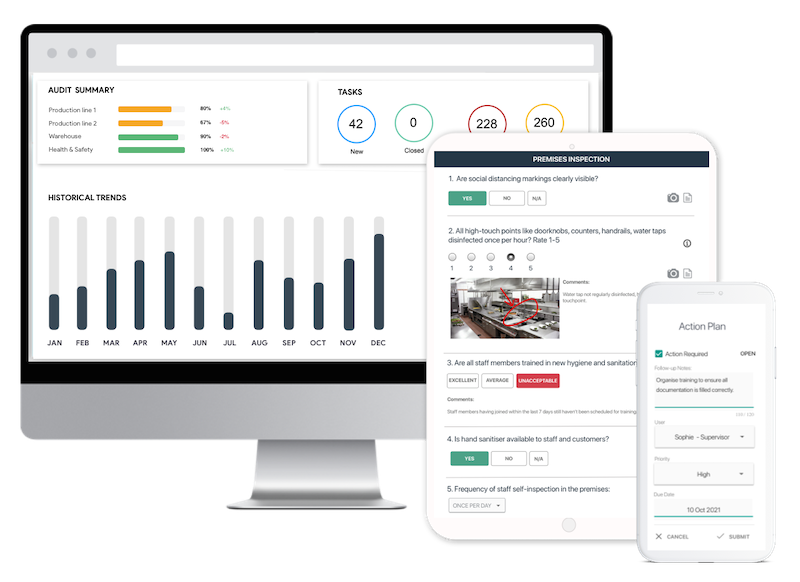
- GoAudits’ user-friendly interface makes it easy to create, edit, and update your warehouse SOP templates, even for non-technical users.
- Choose from a library of pre-built templates for common warehouse tasks, or build your own from scratch using a simple drag-and-drop interface.
- Collaborate with your team in real-time to review and finalize SOPs, ensuring everyone is involved and aligned.
- GoAudits automatically generates detailed reports with insights into your warehouse performance.
- Track key metrics and identify areas for improvement with interactive dashboards.
- Gain valuable insights into recurring issues, trends, and compliance gaps.
- Assign corrective actions and follow-up tasks to ensure issues are addressed promptly.
- Automate workflows to streamline processes and improve efficiency.
- Stay on top of tasks and deadlines with automated notifications and reminders.
Download FREE & Customizable Warehouse SOP Templates
Do you want to make your warehouse SOP documents easy to access and use? Digital checklists accessible on any device can help you implement warehouse SOPs for your teams. GoAudits offers a range of free warehouse SOP templates that you can customize to match your business requirements and industry standards.
- Good Warehouse Practices Checklist
- Warehouse Safety Inspection Checklist
- 5S Warehouse Checklist
- GMP Warehouse Audit Checklist
- GDP Audit Checklist
- Warehouse Inspection Daily Checklist
- Warehouse Storage Checklist
- Warehouse Inspection Checklist Template
- Warehouse Maintenance Checklist
- General Warehouse Safety Checklist
- Warehouse Housekeeping Checklist
- Warehouse Hazards Checklist
- Warehouse Food Safety Checklist
- Warehouse Health and Safety Checklist
- OSHA Warehouse Safety Checklist
- Forklift Pre-start Checklist
- Forklift Operator Shift Takeover / Handover Checks