Product inspections are essential for maintaining quality control across diverse industries. Whether you’re operating in pharmaceuticals, food and beverage, medical devices, cosmetics, or electronics, these inspections are an important checkpoint to ensure that every product meets defined safety, quality, and compliance standards. In sectors where precision and consistency are non-negotiable, they are even more crucial. Product quality inspections help detect defects, verify specifications, and prevent costly recalls or reputational damage. By catching issues early in the supply chain, they ensure consumer safety, regulatory compliance, and brand integrity.
Let’s explore the different types of product inspections, how to choose the right types for your operations, the steps involved in the process, and key tools to facilitate inspections.
- Understanding Product Inspections
- Types of Product Inspections
- How to Choose the Right Product Inspection for Your Business?
- Key Steps in the Product Inspection Process
- Perform Product Quality Inspections with an Inspection Software
- Common Defects Identified During Product Quality Inspections
- Product Inspection vs Process Control vs Product Testing
- FAQs
Understanding Product Inspections
Product inspections are systematic processes of examining and evaluating products to ensure they meet specified quality standards and buyer requirements. This involves checking various attributes such as appearance, construction, function, size, weight, color, and packaging, aiming to detect any defects or non-conformities before the products reach the market or customers. These inspections occur at different stages of the production process: before, during, or after manufacturing.
Why are Product Quality Inspections Essential?
Here are some reasons why product inspections are important:
- They help catch issues before mass production or shipment, preventing faulty products from progressing further. This ensures that only compliant, high-quality products reach the customer, maintaining consistency and reliability in every batch.
- They help mitigate risks such as delays, rework, and recalls. When inspections are part of your process, suppliers are more likely to meet their contractual obligations. This fosters accountability and improves communication across all levels of the supply chain.
- Accurate quality checks prevent the accumulation of defective inventory. With fewer rejected products, you can forecast demand more accurately and manage stock levels efficiently. This leads to smoother operations, optimized storage, and reduced holding costs.
- Regular product inspections ensure your products comply with safety, environmental, and quality regulations, both local and international ones. Failing to meet these can result in penalties, recalls, or legal action.
- Detecting problems early minimizes the need for expensive rework, replacements, or product recalls. It also reduces customer complaints and warranty claims. In the long run, a thorough product quality inspection process lowers operational costs and protects your bottom line.
- Regular product inspections demonstrate your commitment to delivering high-quality, defect-free products and customer satisfaction. This not only builds trust and encourages repeat business but also strengthens your brand reputation in competitive markets.
Types of Product Inspections
Each product inspection type serves a distinct purpose in ensuring your product meets quality, safety, and compliance standards. Here’s a breakdown of the key types of product inspections:
1. Pre-Production Inspection
Before a single item rolls off the line, pre-production inspections help assess the quality and quantity of materials and parts. This inspection also ensures that the correct product specifications and design files are used, preventing defects from the start. It also evaluates factory preparedness, identifying risks related to machinery, workforce, or scheduling.
2. Initial Production Check (IPC)
An IPC occurs once production starts but before mass manufacturing. This product inspection confirms that the factory is following product specifications, using the right materials, and aligning with quality requirements. Any deviation found early prevents costly issues from spreading throughout the batch.
3. During Production Inspection (DUPRO)
During production checks, also known as DUPRO, are typically conducted when 20% to 60% of production is complete. It evaluates consistency, identifies recurring defects, and ensures that corrective actions have been implemented effectively. It reduces the risk of large-scale rework or shipment delays.
4. Final Product Inspection or Pre-Shipment Inspection (PSI)
A finished product inspection, also known as Final Random Inspection (FRI), aims to approve or reject a shipment before it leaves the factory. It is the same step as Pre-Shipment Inspection (PSI), since it is your final checkpoint to catch issues before finished products reach your customers. It is typically conducted when production is 100% complete and at least 80% is packed. It verifies product conformity to specifications, quantity, workmanship, labeling, and packaging.
5. Container Loading Inspection
This type of product inspection focuses on how goods are packed and secured in shipping containers. It checks the quantity, packaging integrity, loading method, and container condition. Proper loading prevents damage in transit and reduces liability risks.
6. In-Line Inspection
In-line inspections occur at specific points during the production process. These spot checks help detect issues as they arise, allowing for immediate correction without halting operations. This method is efficient for maintaining continuous quality control.
7. Production Monitoring
It’s a continuous product inspection approach that involves deploying a quality control expert at the factory for ongoing supervision. The inspector monitors each step, reports daily, and ensures standards are consistently met. It improves communication, reduces error rates, and supports long-term supplier development. Unlike DUPRO, which is a one-time spot-check, production monitoring offers uninterrupted quality assurance.
Type of product inspections | Purpose | When to use |
Pre-production inspection | Verify raw materials and components before production begins | Before production starts or when sourcing new suppliers |
Initial production check | Inspect the first batch of production | At the start of mass production, especially for new products or first-time suppliers |
During production inspection | Assess product quality during ongoing production | For large orders, tight deadlines, or repeated quality issues |
Final or Pre-shipment inspection | Confirm product quality before shipment | Before releasing the final payment or approving shipment |
Container loading inspection | Ensure products are loaded correctly and safely into containers | At the time of product loading, especially for fragile or high-value items |
In-line inspections | Conduct real-time checks at critical production stages | For continuous production lines or products requiring close tolerance |
Production monitoring | Provide continuous oversight throughout the production cycle | For high-stakes production, sensitive timelines, or quality-critical products |
How to Choose the Right Product Inspection for Your Business?
To choose the right product inspection, follow a structured approach tailored to your business model, product type, and risk tolerance.
Assess Your Product’s Risk Level
Begin by evaluating the inherent risks associated with your product. Consider its complexity, end-use, target market, and potential safety hazards. High-risk products, such as medical devices, electronics, or automotive components, require more stringent inspection protocols than low-risk goods like non-critical apparel or stationery.
Key factors to assess include:
- Safety concerns or regulatory liabilities
- Product complexity or variability
- Historical quality issues or recalls
- Impact of failure on the customer
A clear understanding of risk helps determine inspection depth and frequency.
Understand Industry Standards and Compliance Requirements
Familiarize yourself with the standards that govern your industry and markets. These standards provide a foundation for production inspection criteria and methods.
Commonly used standards include:
- ISO 9001: Overall quality management system requirements.
- ISO 2859: Statistical sampling procedures for inspection by attributes.
- ANSI/ASQC Z1.4: Acceptable Quality Limit (AQL) standards for batch sampling.
- ISO/IEC 17020: Criteria for inspection bodies’ operation.
- Industry-specific guidelines: FDA for medical, CE for EU compliance, etc.
Document all relevant standards to avoid compliance gaps during inspections.
Match Product Inspection Type to Your Business Needs
Align inspection efforts with your operational model and product lifecycle. For instance, startups may need tighter control during the initial production phase, while established manufacturers may focus on batch consistency and cost-efficiency.
Ask yourself:
- Do you need production inspections during production or only before shipment?
- Are you focused on process improvement, compliance, or both?
- Will product inspections be conducted in-house or outsourced?
Define clear goals to guide the choice of inspection type.
Choose the Right Product Inspection Method
Your inspection method should align with your product’s characteristics and critical quality attributes. Each method serves a distinct purpose, and often, a combination of methods yields the best results.
- Visual Inspection: Use visual checks to identify surface defects, cosmetic imperfections, assembly errors, and labeling issues. It’s quick, cost-effective, and suitable for most product types.
- Dimensional Measurement: Measure physical parameters such as size, weight, thickness, and tolerances. This is important for products requiring precise specifications, such as machined components.
- Functional or Performance Testing: Assess how well the product performs under normal or stress conditions. This is essential for electronics, mechanical assemblies, and any item where performance impacts safety or customer satisfaction.
- Non-Destructive Testing (NDT): Detect internal flaws without damaging the product. Common NDT techniques include ultrasonic, magnetic particle, and radiographic testing. It’s ideal for aerospace, automotive, and structural components.
- First Article Inspection (FAI): Conduct FAI on the first product of a new production run. It verifies that manufacturing processes are correctly set up. Crucial for new product launches or after process changes.
- Statistical Sampling: Apply statistical sampling when inspecting 100% of goods is impractical. Use AQL tables to determine sample size and acceptance criteria. Ensures quality while maintaining efficiency.
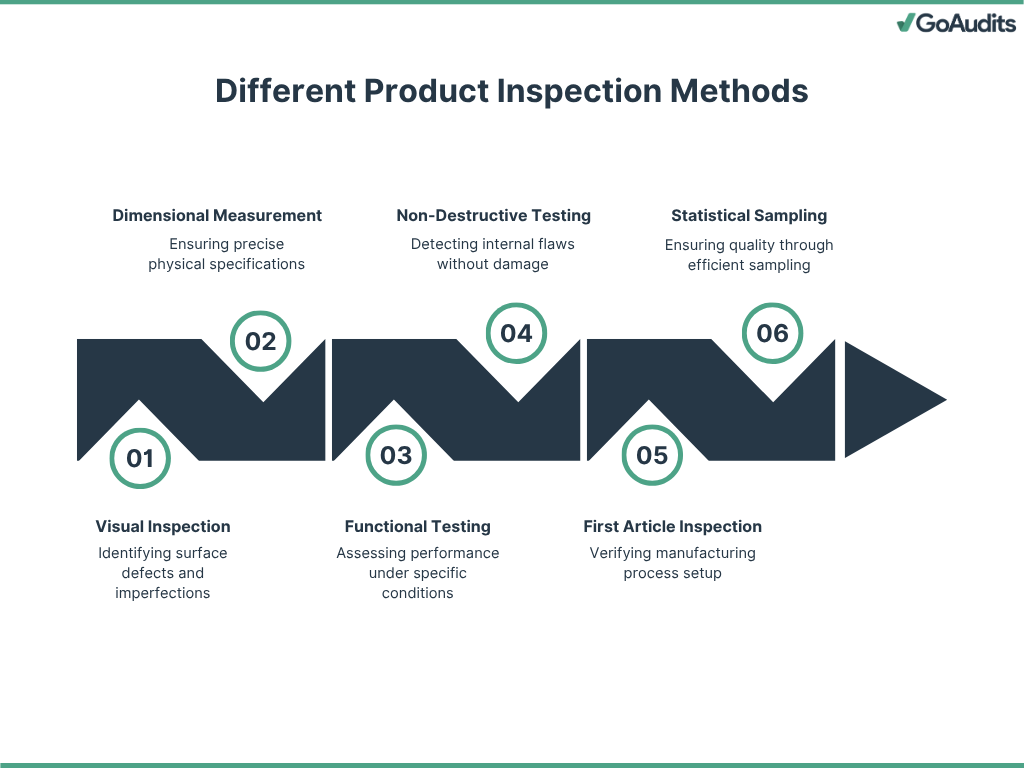
Consider Your Internal Resources and Capabilities
Examine what your internal team can handle. Do you have trained inspectors, calibrated equipment, and documented procedures? If not, limit in-house product inspections to basic checks and outsource the rest.
Evaluate:
- Staff expertise and availability
- Inspection tools and software
- Capacity to handle volume and variability
- Cost-effectiveness of building in-house capabilities
Make honest assessments to avoid compromising inspection quality.
Evaluate Inspection Service Providers for External Inspections
If outsourcing, choose a provider with deep industry knowledge and proven credentials. A reliable inspection partner helps you scale operations while maintaining quality and compliance.
Consider the following:
- Accreditation (e.g., ISO 17020-certified)
- Experience with your product category
- Transparency in reporting and methodology
- Geographic coverage and response time
- Use of standardized checklists and procedures
- Digital tools for real-time data and analytics
Request sample reports and check references before making a decision.
👉 GoAudits transformed Nissin Foods’ quality control by replacing manual, paper-based inspections with a fully digital solution. By digitizing dozens of daily checks across their production lines, Nissin Foods improved audit efficiency, reduced delays, and ensured timely corrective actions. Real-time reporting enabled quick responses to product integrity issues, while the mobile and desktop access allowed seamless data retrieval and sign-offs.
With over 96% completion rates in GMP audits, it helped maintain compliance with HACCP, GFSI, and other global food safety standards. Customized reporting provided actionable insights across facilities. Nissin Foods also benefited from GoAudits’ responsive customer support and tailored system configurations.
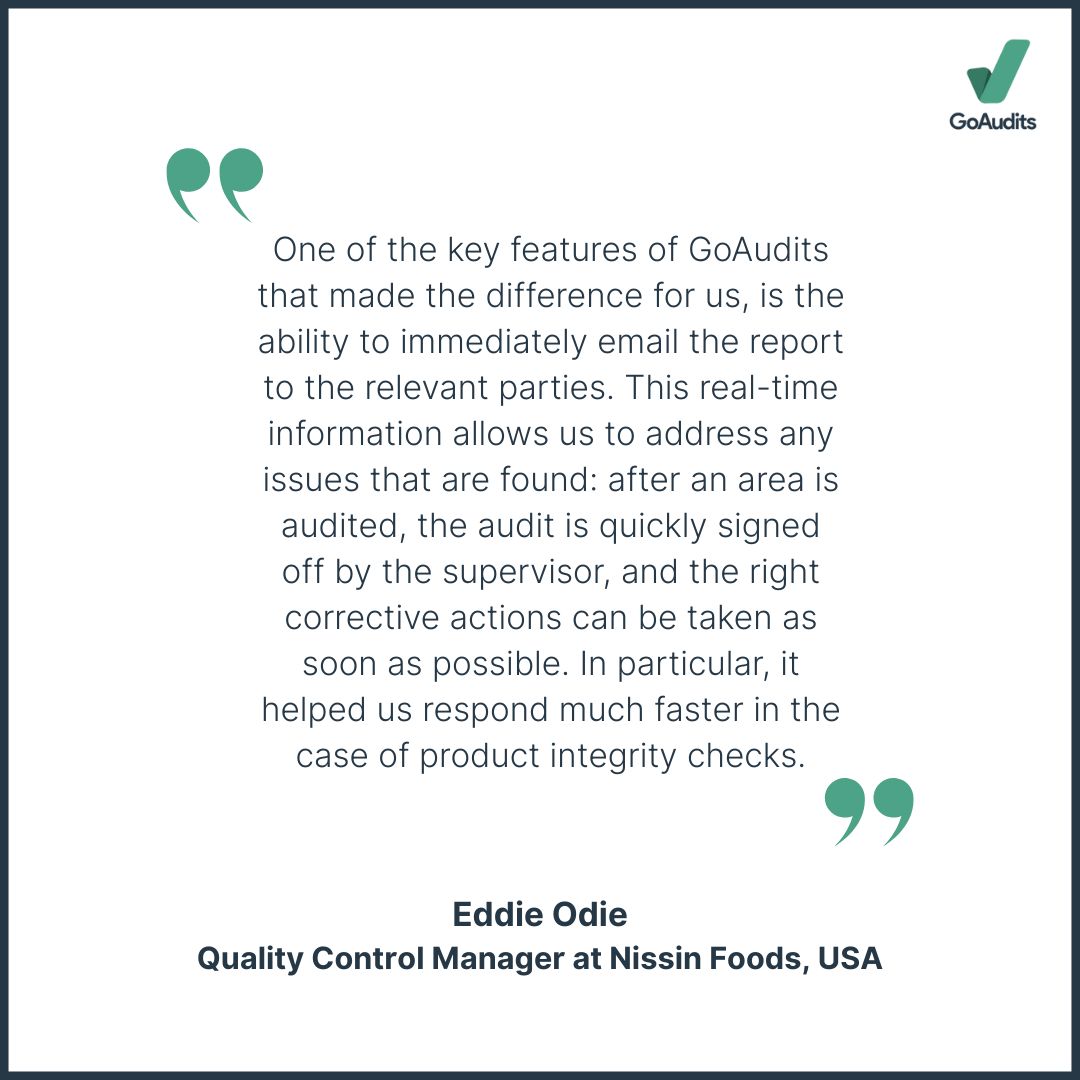
Key Steps in the Product Inspection Process
A robust product inspection process involves the following key steps:
1. Select a Product Sample
Begin by choosing a representative sample from the production batch. This selection must be random to avoid bias. The sample size should align with international inspection standards such as the acceptable quality limit (AQL). The goal is to get a reliable snapshot of the overall product quality.
2. Review Design and Quality Specifications
Before starting the inspection, review the product’s design files, technical drawings, and quality benchmarks. Pay close attention to tolerances, materials, functionality, labeling, packaging, and compliance requirements. This ensures that your inspection process is aligned with product expectations and regulatory standards.
3. Use Digital Checklists to Perform Product Quality Inspections
Use structured digital checklists tailored to your product type. These checklists standardize inspections, reduce errors, and ensure all critical quality aspects are consistently evaluated. Digital checklists also make it easier to log results in real time and maintain data integrity across teams.
👉 Free Resources
You can sign up for free and start using these quality control checklists and product quality control checklists by GoAudits to perform internal product quality inspections.
→ Product Inspection Checklist
→ Process Audit Template
→ Packaging Quality Control Checklist
4. Perform a Visual Inspection
Inspect the product for visible defects such as scratches, discoloration, dents, or assembly flaws. Evaluate workmanship, finish, and packaging integrity. A thorough visual inspection helps detect cosmetic or structural issues that might affect consumer perception or functionality.
5. Document and Report Findings
Capture detailed notes, photos, and measurement data for each defect or non-conformance. Use standardized reporting formats to ensure clarity and comparability across batches. A comprehensive product inspection report provides actionable insights for suppliers and internal stakeholders.
6. Corrective and Preventive Actions (CAPA)
Document all defects and initiate corrective and preventive actions (CAPA) procedures. Define root causes, assign responsibilities, and implement timely fixes. Track CAPA activities to closure and monitor for recurrence. This quality improvement loop helps strengthen your manufacturing processes and reduces future inspection failures.
Perform Product Quality Inspections with an Inspection Software
Performing product quality inspections across multiple teams and sites can quickly become complex and inefficient. With GoAudits quality inspection software, you can simplify the entire quality control process through a unified, mobile-first platform. Capture inspection data effortlessly, generate instant reports, assign corrective actions, and leverage advanced analytics, all without the burden of paperwork or spreadsheets.
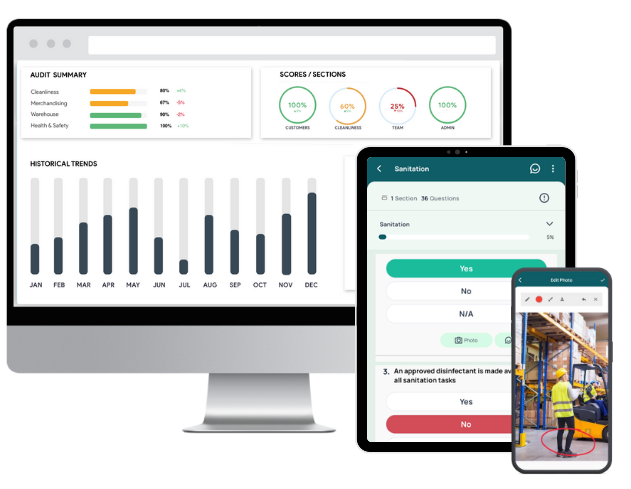
Whether you’re standardizing operations or ensuring compliance, GoAudits helps you take full control of product quality with accuracy, speed, and accountability. Here’s how:
- Access pre-built inspection templates tailored to various industries, build custom checklists using an intuitive drag-and-drop interface, or let us do it for you at no additional cost.
- Conduct product quality inspections on smartphones or tablets, even without internet. Add annotated photos, e-signatures, timestamps, and geolocation for accountability and transparency.
- Automatically generate branded reports at the end of each product inspection, pre-populated with photos, findings, scores, corrective actions, and audit metadata. Share professionally formatted reports instantly with relevant stakeholders.
- Assign tasks directly during the inspection to internal or external teams. Include priority levels, due dates, and instructions for full clarity. Monitor task progress, track completion, and get notified of overdue actions.
- Set rules for report sharing, approvals, task reminders, and escalations. Trigger automatic notifications to ensure the right people act promptly. Use defined hierarchies to enforce accountability and proper oversight.
- View audit scores, trends, and recurring issues across all locations. Schedule audits, monitor action completion, and stay audit-ready always.
At Heat Treating Services Corporation of America, GoAudits replaced paper-based checks with a fully digital audit system and transformed quality control. With five facilities operating around the clock, the company needed a smarter way to monitor precision-driven processes. Earlier, it manually recorded quality data, making trend analysis difficult and time-consuming.
👉 Now, production operators and supervisors conduct checks using mobile devices, enabling real-time visibility and faster issue resolution. GoAudits’ dashboards allow the Quality Assurance team to spot trends, identify missed audits, and take preventive actions before non-conformances occur. As a result, HTS has significantly reduced paper usage, improved process clarity, and strengthened overall quality assurance.
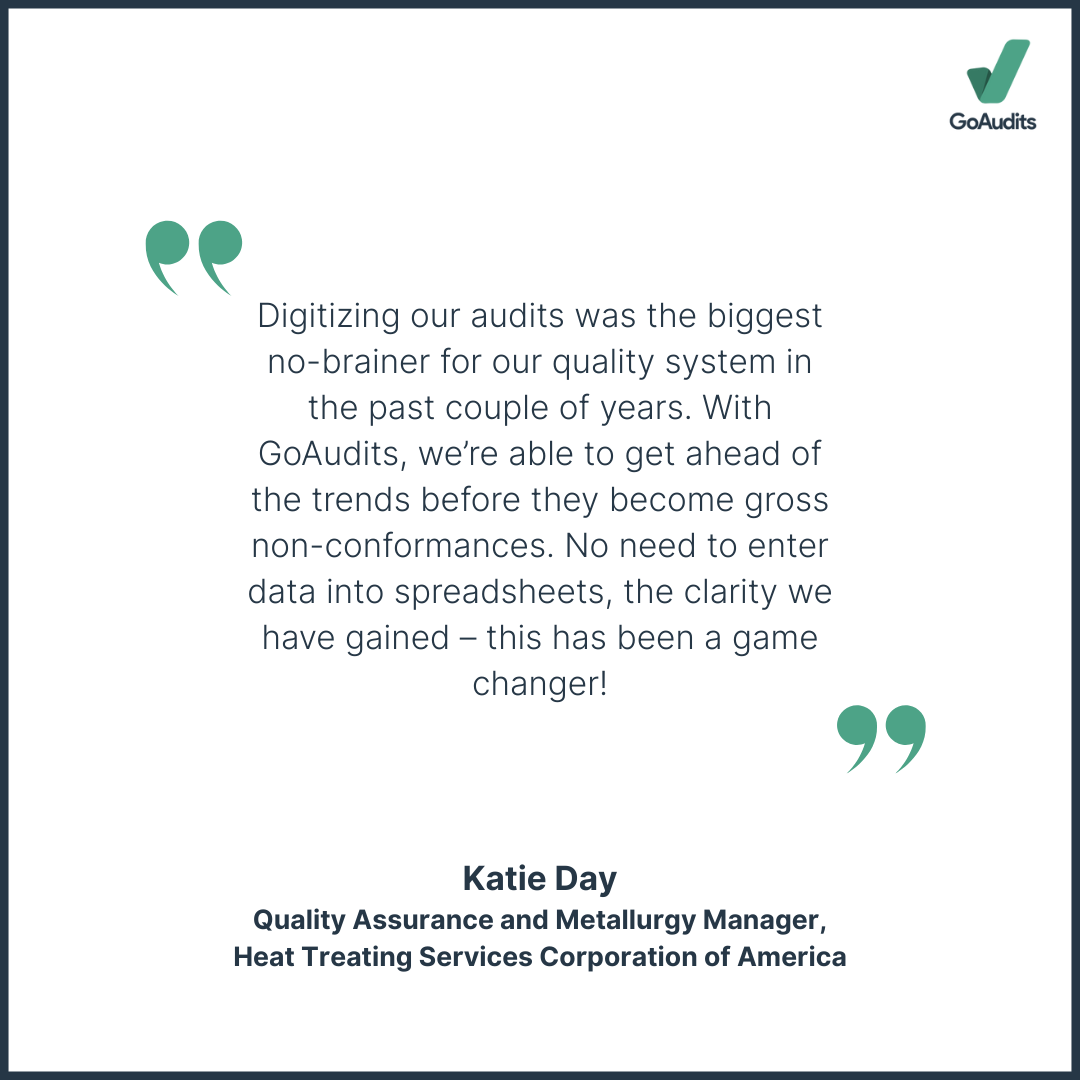
Common Defects Identified During Product Quality Inspections
During product inspections, defects are usually categorized based on their severity: minor, major, or critical. Understanding the distinctions among these categories helps you implement more effective quality control strategies.
Minor Defects
Minor defects are small imperfections that typically do not affect the product’s functionality or performance. However, they may impact the perceived quality or aesthetic appeal. These issues usually don’t make the product unusable, but they can reduce its overall value in the eyes of the consumer.
Although products with minor defects may still be considered saleable, repeated occurrences may signal weaknesses in the production process. Over time, they can lead to customer dissatisfaction or returns if not addressed proactively.
Major Defects
Major defects are more serious and may compromise the product’s usability, functionality, or safety. Products with major defects often fail to meet customer expectations or industry standards and are usually rejected during inspections.
Major defects require immediate corrective action. They can disrupt supply chains, lead to shipment delays, and increase operational costs. Regular inspections and root cause analysis are essential to reducing their occurrence.
Critical Defects
Critical defects pose serious safety risks to the end user or result in regulatory non-compliance. These are the most severe and unacceptable under any circumstances. A single critical defect can result in product recalls, legal liability, and irreparable brand damage.
If even one unit exhibits a critical defect, the entire batch is typically rejected. Immediate escalation and investigation are necessary to determine the root cause and prevent recurrence.
Defect category | Common examples |
Minor | Slight scratches or smudges on non-visible surfaces, minor misalignment of logos or labels, inconsistent stitching or slight discoloration, and dust or small particles trapped in packaging |
Major | Broken or non-functioning components, incorrect dimensions or measurements, loose parts or weak structural integrity, and noticeable cosmetic flaws on visible surfaces, etc. |
Critical | Electrical hazards or exposed wiring, contamination in food or pharmaceutical products, sharp edges or choking hazards in toys, labeling errors with life-threatening consequences, etc. |
Product Inspection vs Process Control vs Product Testing
Understanding the differences between product inspection, process control, and product testing is essential to ensure quality, compliance, and efficiency in manufacturing and production systems, as each targets different stages and aspects of production.
Definition
Product inspection involves examining finished or semi-finished goods to ensure they meet defined quality standards and specifications.
Process control refers to monitoring and managing production processes in real-time to maintain consistency, reduce variability, and prevent defects.
Product testing involves evaluating a product’s performance, safety, durability, or compliance through technical assessments under controlled conditions.
Focus
Product inspection focuses on visible defects, dimensional accuracy, labeling, packaging, and other physical characteristics of the product.
Process control targets process parameters, such as temperature, pressure, speed, and raw material input, to ensure stable and predictable output.
Product testing concentrates on functional behavior under specific conditions, regulatory compliance, or customer performance requirements.
Timing
Product inspection occurs after or during production, typically at checkpoints or before shipment.
Process control is ongoing, applied during production in real-time to prevent deviations.
Product testing may take place before, during, or after production, often in labs or test environments, depending on the objective.
Nature
Product inspection is reactive, detecting non-conformities after they occur.
Process control is proactive, aiming to avoid issues by maintaining process stability.
Product testing is both proactive and diagnostic, often used to validate product design or identify root causes of failure.
Purpose
Product inspection ensures products meet specifications before reaching customers.
Process control maintains quality throughout production, improving efficiency and reducing waste.
Product testing validates product quality, compliance, performance, and suitability for use or market entry.
Example
- Product Inspection: Checking a batch of smartphones for cosmetic defects and screen functionality before packaging.
- Process Control: Monitoring injection molding temperature and pressure to ensure plastic components maintain uniform strength.
- Product Testing: Conducting drop tests on smartphones to verify durability against accidental falls.
Setting
Product inspection takes place in warehouses, production lines, or quality control rooms.
Process control is integrated within production environments, utilizing sensors, data systems, and control charts.
Product testing occurs in laboratories or simulated environments, often using specialized equipment and standardized protocols.
FAQs
A product audit evaluates the overall quality, compliance, and performance of a finished product against defined specifications, standards, and customer requirements, often as part of a broader quality management system. A product inspection is a more focused, task-specific activity that involves examining, measuring, or testing individual items or batches to identify defects or deviations from set criteria. While an audit assesses systemic effectiveness and consistency, a product inspection detects immediate, tangible flaws, making each process distinct in scope, purpose, and timing.
PPI is carried out before manufacturing begins and focuses on verifying the quantity and quality of raw materials and components, ensuring they meet product specifications, and assessing factory readiness, production line setup, and the supplier’s understanding of requirements. Its main goal is to prevent the use of substandard materials, identify potential issues before production starts, and minimize risks of supply chain disruptions or delays by inspecting materials, reviewing equipment, and evaluating quality control systems.
IPC takes place at the onset of production, typically when the first batch or up to 20% of output is completed, and centers on inspecting the first finished products, confirming that the manufacturing process aligns with specifications, and checking product appearance, functionality, and packaging. IPC aims to detect and address problems early in production, ensure initial output quality before mass manufacturing proceeds, and provide an early warning for defects or non-compliance by evaluating production samples, reviewing methods and capacity, and performing functional and appearance tests on initial products.