Quality control in packaging is essential not only for packaging manufacturers but also for any business that relies on packaging to deliver products safely and consistently. Whether you’re producing consumer goods, pharmaceuticals, or electronics, the integrity of your packaging directly affects product quality, regulatory compliance, and customer satisfaction. Packaging inspections can help maintain integrity by identifying defects, inconsistencies, and compliance issues early in the production process. Packaging quality inspections prevent costly recalls, reduce waste, and ensure that goods reach the end user in optimal condition
This article will explore why packaging compliance inspections are essential for building operational efficiency, safeguarding brand reputation, and meeting industry standards.
- Understanding Packaging Inspections
- Types of Packaging Inspections & How They Ensure Quality Control
- Common Defects and Issues Identified During Packaging Audits
- Key Factors to Consider in Packaging Inspection
- Packaging Inspection Procedures
- Conduct Efficient Quality Inspections with GoAudits
- Free Packaging Quality Control Checklists
- What are the Benefits of Performing Regular Packaging Audits?
Understanding Packaging Inspections
Packaging inspections, or packaging audits, are important checkpoints within the supply chain. They involve systematic inspections of packaging materials and processes to verify that they meet specific standards and requirements, ensuring that products are securely and accurately packaged to maintain quality, safety, and compliance.
These inspections help prevent product damage, contamination, and regulatory issues, safeguarding brand reputation and customer satisfaction. Packaging audits assess various aspects, including structural integrity, seal strength, label accuracy, compliance with industry regulations and standards, and more.
The four main types of packaging are:
1. Primary packaging comes into direct contact with the product itself. Its main purpose is to protect the product and maintain its quality. Examples include blister packs, bottles, and wrappers.
2. Secondary packaging groups together primary packages for easier handling, storage, and transport, often for protection and branding purposes. Examples include cartons that hold multiple bottles or boxes.
3. Tertiary packaging is used for bulk handling, storage, and transportation of goods, grouping secondary packages together. Pallets wrapped in stretch film are a common example.
4. Ancillary packaging refers to additional materials used to support, protect, or present the product, such as labels, adhesives, cushioning, or straps.
Packaging inspections are strategically conducted at multiple stages within the supply chain to ensure consistent quality and compliance:
- Initial Production Checks (IPC): Performed at the onset of production to verify that packaging materials and processes meet specified standards.
- During Production: Ongoing inspections monitor the packaging process to identify and rectify issues in real-time.
- Pre-Shipment Inspections (PSI): Conducted when production is at least 80% complete, these inspections assess the final product’s packaging for defects, ensuring that it meets quality standards before shipment.
- Receiving Inspections: Upon arrival at distribution centers or retail locations, the packaging is inspected to confirm that it has remained intact and compliant during transit.
These inspections can take place at manufacturing facilities, warehouses, ports, and distribution centers, depending on the specific stage and requirements of the supply chain.
Which Industries Rely on Packaging Inspections?
Packaging inspections are essential across various industries, including the following:
- Food and Beverage: Ensuring packaging prevents contamination and preserves product freshness. Defective packaging can lead to health risks and regulatory non-compliance.
- Pharmaceuticals and Medical Devices: Maintaining sterility and preventing contamination are critical. Packaging inspections verify seal integrity and compliance with stringent regulatory standards.
- Electronics: Protecting sensitive components from environmental factors and ensuring packaging prevents electrostatic discharge.
- Automotive and Transportation: Ensuring that parts are securely packaged to prevent damage during transit, which could affect vehicle safety and performance.
- Consumer Goods: Verifying that packaging is both protective and appealing, maintaining brand image and customer satisfaction.
Types of Packaging Inspections & How They Ensure Quality Control
Let’s explore the different types of packaging quality inspections.
Visual Inspection
They involve examining packaging for surface-level defects such as scratches, dents, misprints, or contamination. This process can be conducted manually or with the help of automated vision systems. Regular visual inspections help in promptly identifying and rectifying issues, preventing defective products from reaching consumers.
Dimensional Inspection
They ensure that packaging components adhere to specified measurements and tolerances. Using tools like calipers, micrometers, or coordinate measuring machines (CMMs), it verifies parameters such as length, width, height, and thickness. Accurate dimensions are crucial for proper fit, stacking, and compatibility with automated systems, minimizing material waste and operational disruptions.
Mechanical Testing
Mechanical testing assesses the strength and durability of packaging materials under various stress conditions. Tests such as compression, drop, and vibration evaluate the packaging’s ability to protect contents during handling and transportation. Implementing mechanical testing helps in identifying potential weaknesses, ensuring that packaging can withstand real-world challenges and maintain product safety.
Material Testing
Material testing examines the physical and chemical properties of packaging materials to ensure they meet quality standards. This includes evaluating tensile strength, moisture resistance, and barrier properties against gases or contaminants. Such testing is vital for determining the suitability of materials for specific products, especially in industries like food and pharmaceuticals where material integrity directly impacts product safety.
Labeling Inspection
Labeling inspection verifies the accuracy, legibility, and placement of labels on packaging. It checks for correct information, such as product details, barcodes, and regulatory compliance marks. Automated systems often utilize optical character recognition (OCR) and barcode verification tools to detect errors like smudging, misalignment, or incorrect data. Ensuring proper labeling is important for traceability, legal compliance, and consumer trust.
Type of Inspection | Purpose |
Visual Inspection | Detects surface-level defects |
Dimensional Inspection | Verifies measurements and tolerances |
Mechanical Testing | Assesses strength and durability under stress |
Material Testing | Evaluates physical and chemical properties |
Labeling Inspection | Confirms label accuracy and compliance |
Common Defects and Issues Identified During Packaging Audits
Below is a structured overview of common issues uncovered during packaging audits:
Physical Damage and Appearance Issues
Physical defects often arise from mishandling, inadequate materials, or improper packing techniques. Common issues include crushed or deformed packaging, tears, punctures, or abrasions, contaminated surfaces, and color inconsistencies. These defects not only affect visual appeal but can also lead to potential spoilage or damage to products.
Labeling and Marking Errors
Accurate labeling is critical for compliance, traceability, and consumer information. Errors in this area can lead to regulatory issues and customer dissatisfaction. Common labeling defects include incorrect or missing barcodes, misprinted information, illegible text or graphics, and non-compliance with labeling regulations.
Assortment and Component Issues
Ensuring the correct assortment and inclusion of all components is vital for product functionality and customer satisfaction. Common issues identified during packaging audits include missing components, incorrect assortment, and inadequate cushioning or protective materials. These issues often stem from lapses in the packing process or miscommunication of packaging requirements.
Material and Structural Issues
The choice of packaging materials and structural design directly impacts product protection and shelf life. Common material and structural defects include the use of substandard materials, inadequate sealing, and structural weaknesses.
Regulatory, Safety, and Hygiene Issues
In the food industry, packaging must adhere to strict regulatory standards to ensure consumer safety. Common issues identified during audits include non-compliance with food safety standards, contamination risks, improper storage conditions, and pest ingress.

Key Factors to Consider in Packaging Inspection
Here’s a complete guide to the key factors you should consider in a packaging inspection:
Product Type and Characteristics
The nature of the product significantly influences packaging requirements. Key considerations include fragility, perishability (perishable goods need packaging that maintains appropriate temperatures and humidity levels), chemical sensitivity, and size and shape (look for unusual dimensions).
Regulatory and Safety Requirements
Compliance with local and international regulations is non-negotiable. Key aspects of packaging compliance inspections include material safety, labeling standards, and environmental regulations. Staying updated with regulatory changes is essential to maintain compliance and avoid legal repercussions, in addition to performing regular packaging audits.
Environmental Conditions
Packaging must withstand various environmental factors during storage and transportation. Environmental testing ensures packaging durability and product protection under expected conditions by checking temperature fluctuations, humidity, moisture, and exposure to light.
Logistics, Shipping, and Handling
Efficient packaging facilitates smooth logistics and minimizes damage risks. Testing packaging under simulated shipping conditions for stackability, weight considerations, and ease of use, can identify potential weaknesses and areas for improvement.
Functionality and Usability
Packaging should enhance user experience and product accessibility. Prioritizing ease of opening, resealability, functionality, and clear instructions ensures customer satisfaction and can influence repeat purchases.
Packaging Inspection Procedures
A structured inspection process follows a four-step approach: preparation, conducting the inspection, reporting and documentation, and corrective action with follow-up.
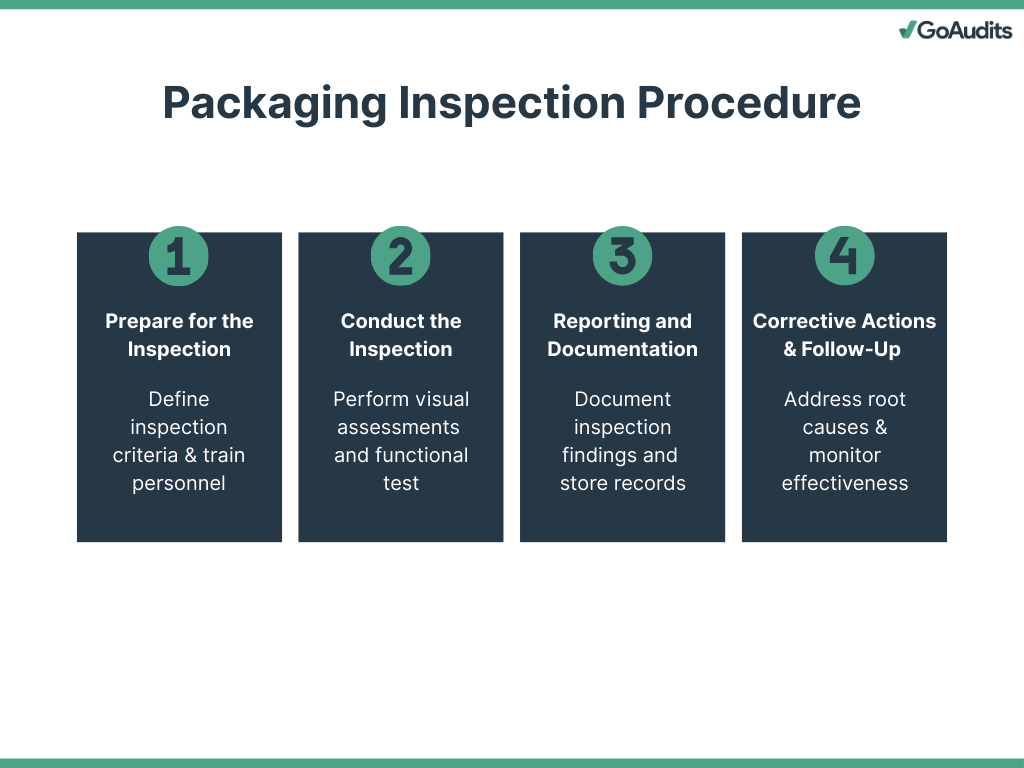
Preparation
It begins with clearly defining inspection criteria based on product specifications, regulatory guidelines, and customer requirements. These standards guide the inspection process and set the benchmarks for quality. Detailed checklists covering all aspects of packaging, including materials, sealing, labeling, and protective features are essential.
Ensure that inspection personnel are adequately trained in both the technical aspects of the inspection and the use of any specialized tools. Calibration of equipment must be performed regularly to ensure measurement accuracy and consistent results.
Conducting the inspection
It requires a methodical and systematic approach. Begin with a visual assessment of packaging components, checking for visible defects such as dents, tears, or misaligned labels. Use precise measuring tools to verify that dimensions are within acceptable tolerances. Perform functional tests where applicable, such as pressure, drop, or vibration tests, to assess the packaging’s performance under stress.
Label verification is also essential. Check for correct information, legibility, and compliance with regulations. Apply statistically valid sampling methods to ensure your inspection is representative of the full batch.
Reporting and documentation
It plays a crucial role in ensuring traceability and accountability. Document all findings in detail, noting any deviations from the established criteria. Photographic evidence of defects enhances the accuracy and clarity of records.
Inspection reports should be structured and comprehensive, including descriptions of procedures followed, results obtained, and corrective actions taken. Records must be stored securely and made accessible for internal reviews or external audits.
Corrective action and follow-up
It addresses the root causes of any issues identified during the inspection. Conduct a thorough root cause analysis to pinpoint underlying problems. Once identified, implement corrective actions that may include process adjustments, retraining staff, or changing suppliers.
Preventive measures should also be established to reduce the risk of recurrence. Finally, continuously monitor the effectiveness of these corrective actions through regular reviews and inspections.
Conduct Efficient Quality Inspections with GoAudits
GoAudits quality inspection software transforms the way businesses conduct quality inspections by offering a comprehensive, all-in-one platform designed for accuracy, efficiency, and accountability, without the need for training or complex setup. GoAudits packaging manufacturing inspection app streamlines packaging inspections by digitizing every step, from preparation to execution to documentation and implementation and tracking of corrective actions.
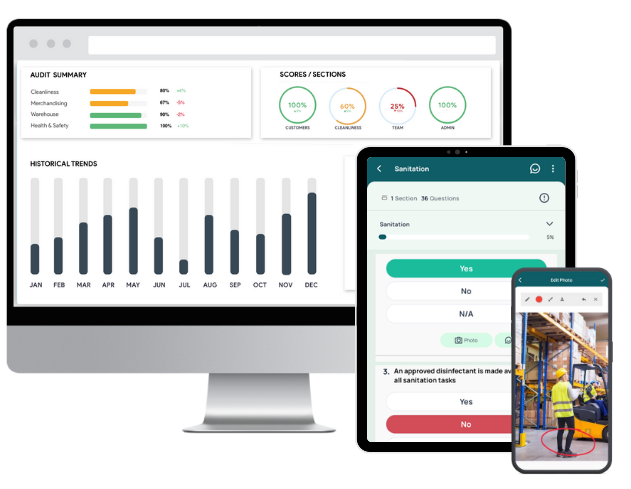
- Start from ready-to-use templates or build custom checklists with a drag-and-drop editor. Submit your existing checklists in any format and we will digitize them for you at no additional cost.
- Use a simple, intuitive mobile app to perform packaging inspections, even when offline. Capture and annotate photos as visual evidence, and include timestamps, geolocation, and e-signatures for full accountability.
- Schedule packaging audits, track their status, and ensure timely execution across teams and locations.
- Automatically generate reports instantly after the completion of each packaging quality inspection, including attached photos, corrective actions, timestamps, and user details.
- Customize packaging inspection and quality control reports to meet your branding requirements and share them instantly via email with the relevant team members.
- Assign corrective actions during packaging inspections to internal or external team members. Include priority, due date, and task description for clear accountability, and track overdue actions and their completion status.
- Define your company hierarchy to set up workflows for task approvals, report distribution, and trigger email notifications.
- View audit performance and scores across locations and teams. Use smart dashboards to track and monitor historical trends and identify recurring issues and areas for improvement, facilitating quick decision-making.
Nissin Foods, the first cup noodle manufacturing brand in the US, leveraged GoAudits manufacturing inspection software to transform its quality control processes. Nissin Foods conducts dozens of audits daily across manufacturing sites to ensure compliance with global food safety standards like GMP, HACCP, and GFSI. These inspections cover production lines, product quality, packaging, facility areas, and incident tracking.
👉 GoAudits helped Nissin Foods achieve a remarkable completion rate of over 96% for GMP audits.
Customizable reporting tools provided valuable insights into audit trends, and dedicated customer support ensured a seamless onboarding experience.
Free Packaging Quality Control Checklists
GoAudits offers a wide range of packaging quality control checklists. Sign up for free and start using these checklists.
- Packaging Quality Control Checklist
- Packaging Material Vendor Audit Checklist
- Product Inspection Checklist
- SQFI Manufacturing of Food Packaging Checklist
- BRC Audit Checklist Product Control (Clause 5)
- GMP Inspection Checklist
What are the Benefits of Performing Regular Packaging Audits?
Below are the key benefits of implementing regular packaging audits:
- Regular packaging audits verify that packaging materials and methods effectively safeguard products during transportation, storage, and handling to maintain product quality and consumer safety. This is particularly crucial for perishable goods, pharmaceuticals, and electronics, where compromised packaging can lead to contamination or damage.
- Advanced inspection systems used during packaging audits can detect minute defects that manual checks might overlook. Identifying issues such as misaligned labels, seal weaknesses, or material inconsistencies early in the process prevents defective products from reaching consumers, preserving brand reputation and reducing returns.
- Packaging audits often incorporate traceability mechanisms like barcodes and RFID tags, enabling tracking of products throughout the supply chain. This facilitates quick responses to recalls, ensures authenticity, and aids in inventory management.
- By identifying inefficiencies and material wastage in packaging processes, packaging audits contribute to cost savings. They help in optimizing packaging designs, selecting appropriate materials, and streamlining operations, leading to reduced material costs and environmental impact.
- Consistent packaging quality assures customers of a brand’s commitment to excellence. When products arrive intact and as expected, customer satisfaction increases, fostering loyalty and positive word-of-mouth.
- Implementing improvements based on audit findings can enhance efficiency in packaging operations, reduce downtime, and accelerate time-to-market for products.
- Packaging audits ensure compliance with industry regulations and standards, mitigating the risk of legal penalties and product recalls. They verify that labeling, material usage, and packaging processes comply with relevant laws.